A water treatment solution consisting of leading edge engineering design, 3D modelling and project management, alongside offsite manufacturing, has enabled Britvic to expand its production capabilities at its Leeds UK facility from 70m³/hr to 200m³/hr.
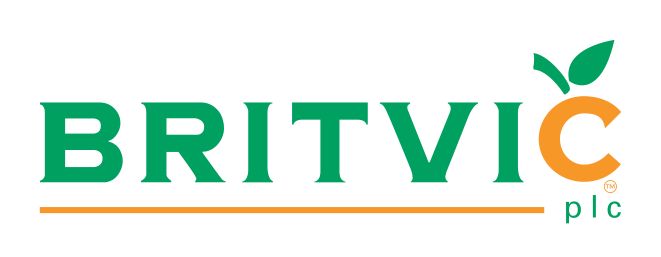
Envirogen Group was responsible in providing a complete water treatment solution from initial design to manufacture, installation and plant commissioning, using an expert team of engineers and project managers. The solution incorporates the latest chlorine generation and ion exchange techniques, delivering a long-term and efficient operation that allows production to increase in line with Britvic’s business growth objectives.
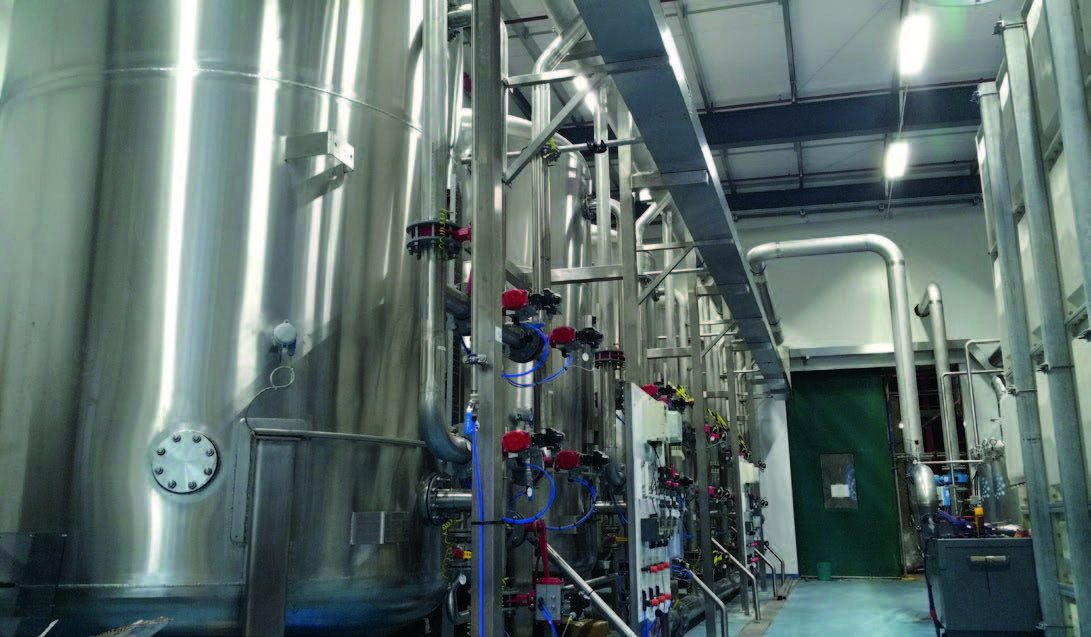
According to Envirogen’s UK and European CEO, Bill Denyer, following the closure of its operation at Chelmsford in Essex, UK, Britvic was looking to expand the plant in Leeds to accommodate additional product lines and scale up production output.
“The existing incoming water treatment capacity, running at 70m³/hr, was the bottleneck to the Leeds plant reaching its full potential,” explains Denyer. “As the incoming water is used directly in the final product, the system has to comply with demanding safety and quality regulations as well meeting the increased scale of production. Britvic needed to expand output without disrupting its existing operation and approached Envirogen to design a water treatment solution.”
An additional challenge was the short timeframe Britvic had for removing machinery from the Chelmsford site. With a new building to house the water treatment process in Leeds under construction, and a live production environment that couldn’t be compromised, the pressure was on to find an effective solution to expand production capabilities without impacting on the daily output from the site. Envirogen appointed a dedicated and expert project team to ensure that the development met key milestones and was completed to budget, along with seamless integration into the manufacturing environment.
State-of-the-art 3D modelling enable virtual walkthroughs
Denyer continues: “With only four weeks to factory shutdown, we removed the equipment from the old site to be stored at our state of the art manufacturing and global distribution centre in Alfreton, Derbyshire.”
“Detailed 3D models were created, using the plans from the new building. The Britvic team were able to see the plant in its entirety within the structure of the new building, whilst drilling down to view individual components in detail.”
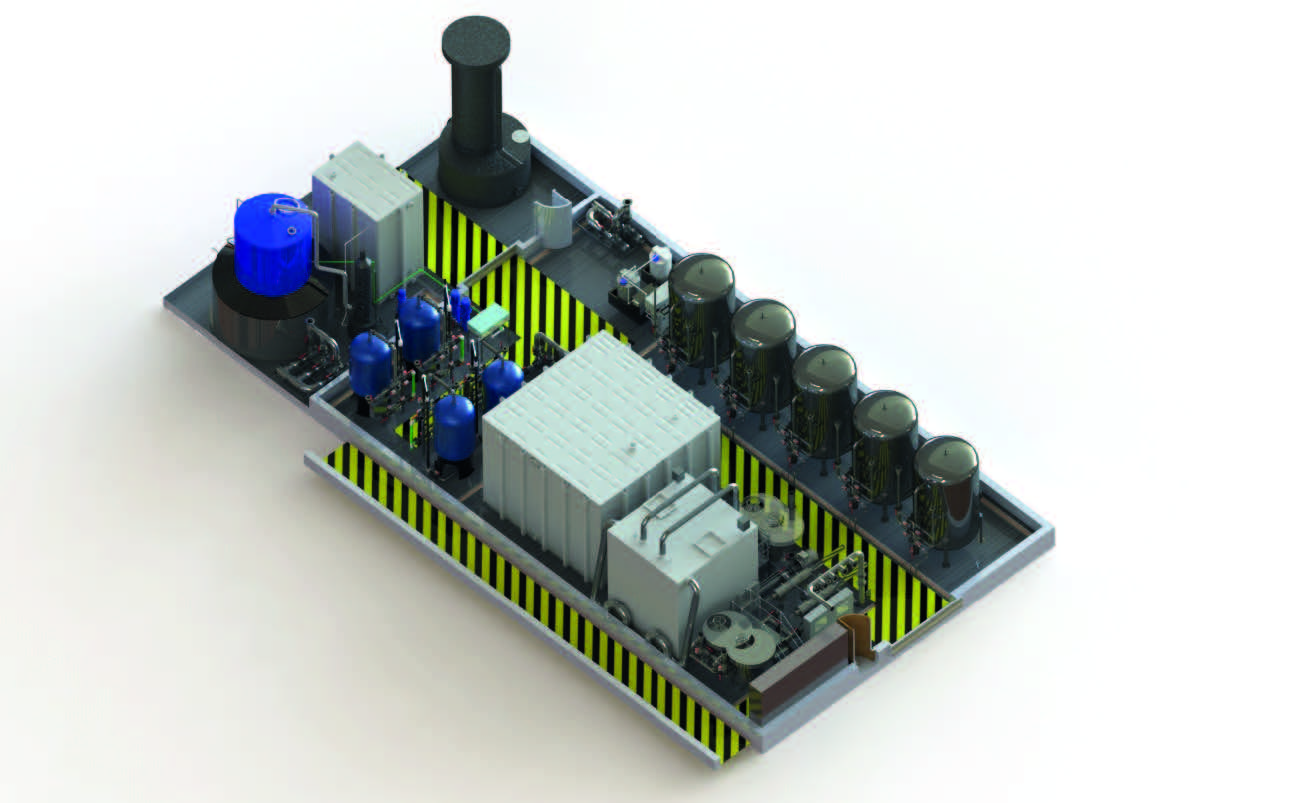
During the construction phase, Envirogen built the turnkey solution at its manufacturing centre, making use of the advanced design and fabrication facilities available onsite. The client viewed the solution as it was being built and completed acceptance testing on key parts of the solution. With complete project transparency Britvic were able to see that the tasks were progressing according to plan, and within the scope agreed.
Once the building work was completed, the water treatment system was transported to Leeds for integration and plant commissioning. As the majority of acceptance testing was carried out before the system was brought to site, the plant was installed with no impact on the daily production output, enabling Britvic to continue to meet its production targets.
A treatment solution that spans the production cycle
To produce the highest water quality for direct inclusion within the product, as well as regeneration and backwash tasks, the final water system included:
- Ion exchange dealkalisation beds, making use of regeneration beds to reduce acid costs.
- Electrochlorination and dosing equipment, producing chlorine on demand with no need for manual handling and storage.
- Activated carbon beds, complete with steam sterilisation.
- UV sterilisation.
- 10μ and 1μ absolute cartridge filtration system using long life Envirogen brand cartridges.
- Fully automated Siemens control panel.
Envirogen continues to service and maintain the plant through the PureCare service plan. The plan provides valuable peace of mind, delivering 24-hour onsite call out and ensuring the system delivers long lifetime value.
“We chose Envirogen Group because of its stand-out expertise and experience in our sector. The 3D modelling was hugely beneficial because we were able to accurately visualise the plant and all its components, and address issues before build began. This was particularly important as the solution needed to integrate with existing facilities.”
“Having the system constructed offsite meant that we were able to run both the building and plant construction at the same time. We visited the manufacturing centre frequently to see the build in process and complete our user testing and the Envirogen team were really helpful in providing training so that the team were ready to run the equipment. We are delighted with the finished system and we’re excited about using it to its full potential.”
John Marshall, Project Manager, Britvic.
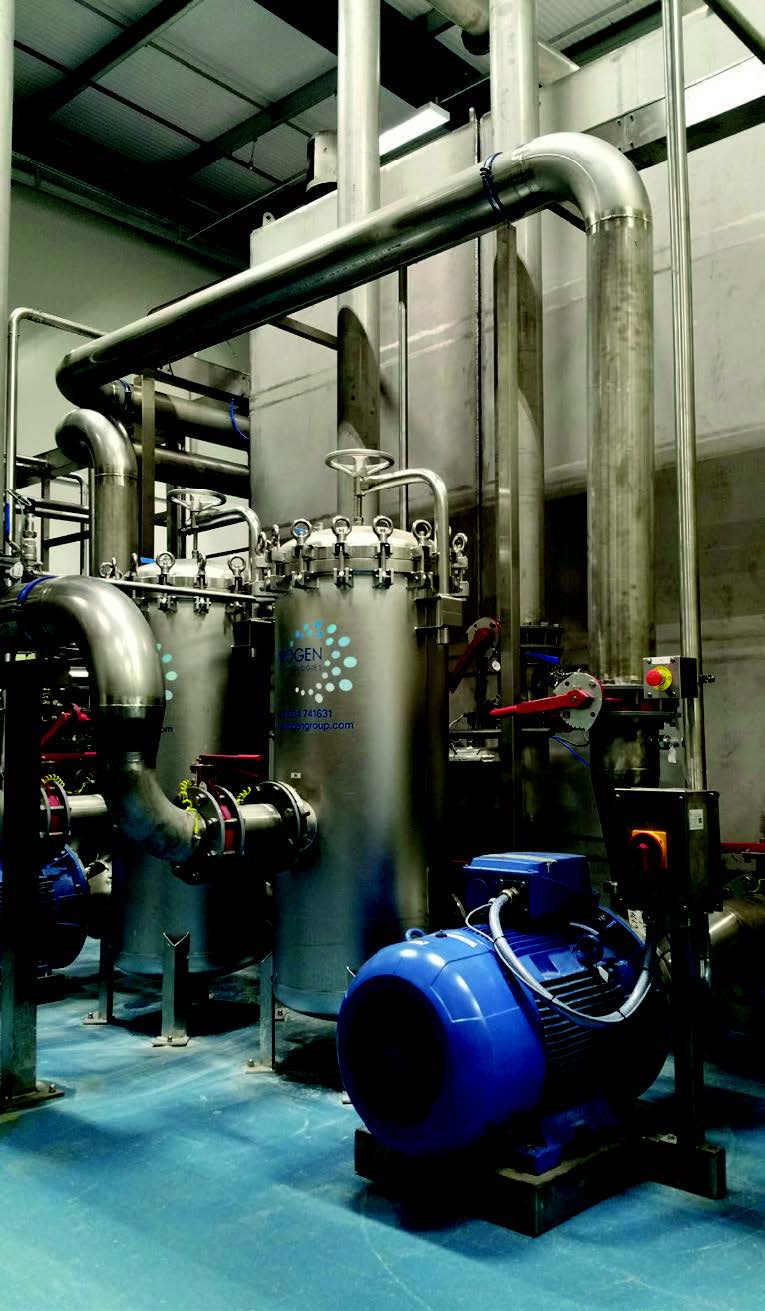
Read more about Britvic water treatment and process filtration solutions:
Key outcomes
- The project was completed on time and to budget with no downtime required for integration
- Existing treatment equipment was reused and repurposed enabling significant cost savings
- The Leeds plant is able to process 200m³/hr of incoming water, tripling the previous production capability
- Since plant commissioning in October 2015, the plant is using incoming water at a rate of 100m³/hr, enabling Britvic to increase output from the site.
For a free assessment to evaluate water treatment and process filtration solutions for your site, contact our team of expert engineers
About the client
Britvic is a leading soft drinks company, with operations in Great Britain (GB), Ireland, France and Brazil. Britvic manufactures a range of its own brands, including Robinsons, Tango, J2O and Drench as well as PepsiCo’s soft drinks, including Pepsi and 7UP. Britvic is the largest supplier of branded soft drinks and the second largest supplier of carbonated soft drinks in GB.
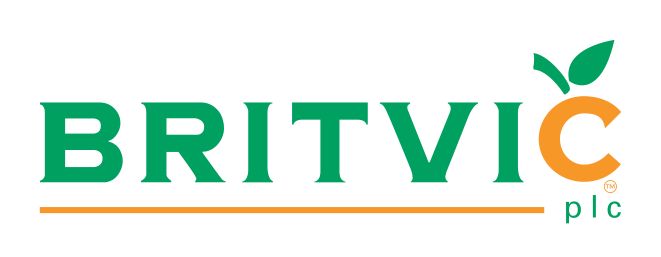