In March 2020, microLED developer Plessey signed an exclusive agreement with Facebook to develop new technologies for use in consumer-ready augmented reality (AR) glasses. This agreement would lead to a large increase in Plessey’s fabrication output and although the manufacturing capacity existed, the ultra-pure water systems, needed to clean tools on the fabrication line, were limited. Following a routine health check, Envirogen Group proposed an upgrade that would double process water production, saving over £1 million when compared to a new installation. The project that followed would see an entire industrial water treatment process brought back on-line within six months, to stringent ASTM standards, in the middle of a national lockdown.
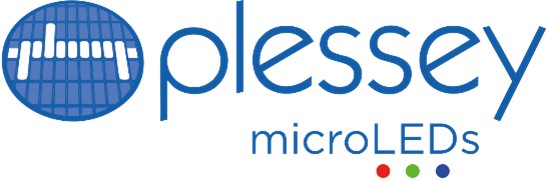
From filtration to water treatment
MicroLED manufacturing is a precise and highly specialised process, over 60 separate fabrication tools are used in the line, each requiring a flow of ultra-pure water to ensure contamination-free end products. Even a small amount of residue can cause product failure, for this reason, water streams must reach the stringent ASTM guidelines for ultra-pure water used in the electronics and semiconductor industries.
As a leading manufacturer of microLEDs and semiconductors, Plessey had the manufacturing capacity and experience to embark on this important collaboration with Facebook. However, a bottleneck in the ageing industrial water treatment process meant that only half the required ultra-pure water could be sent to the fabrication line. The ultra-pure water systems on site were installed over 20 years ago and a significant proportion had been taken out of service when they were no longer needed. With new business, the entire industrial water treatment process needed to be brought back online and futureproofed to ensure reliability.

“We already had an existing relationship with Plessey, supplying process filtration products for another area of the business,” explains Bill Denyer, UK and European CEO, Envirogen. “When we heard that the site needed to scale up its water treatment capacity, we offered to run a health check on the existing system, to see whether the older lines could be used to produce the required water volume and specification.”
“Although this was an important and valuable project for Plessey, it seemed uneconomical to install new ultra-pure water systems if the existing industrial water treatment process could be upgraded to meet the required standards and outputs without compromising quality. The new manufacturing output would demand 30m³ per hour of ultra-pure water, but the water also needed to meet the ASTM standards for electronics manufacturing, which is renowned for being the toughest across all industry sectors.”
“We ran a comprehensive and thorough audit on the entire system, from incoming water streams to the final purified output and benchmarked this against the new requirements. From this evaluation, we recommended a cost-effective refurbishment that would deliver the water quality and volume needed without investment in a new water treatment system.”
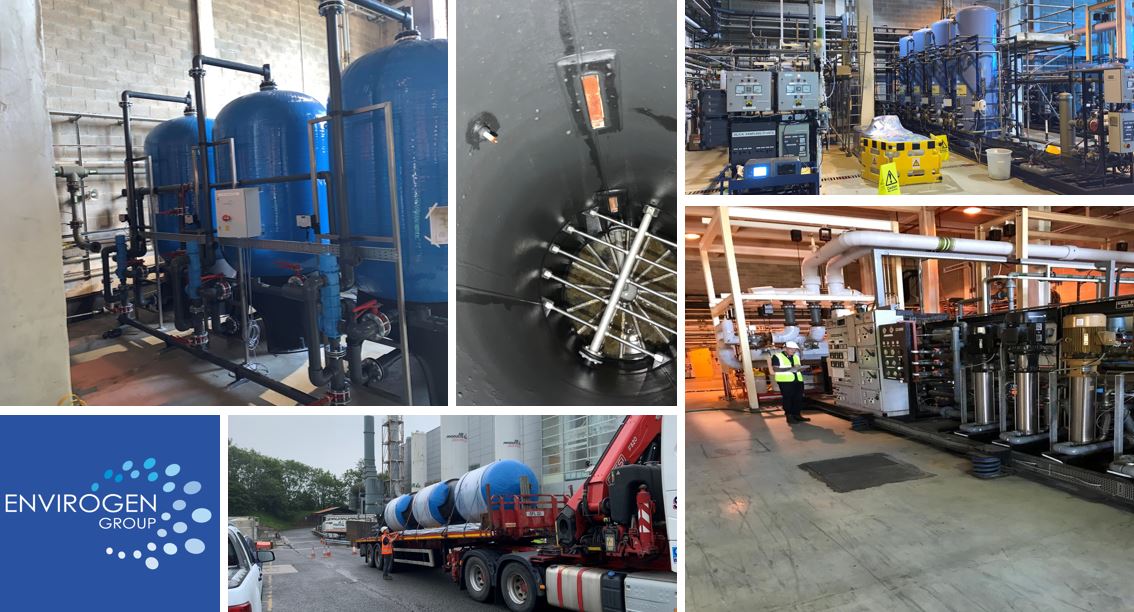
Delivering turnkey solutions in a lockdown
As the health check was completed, the Covid-19 lockdown restrictions commenced but detailed discussions continued online. Plessey went out to the market and Envirogen was successful in the competitive tender process against several other water treatment solutions providers, including the original equipment supplier.
“We really valued the team’s honesty during the health check,” said James Russell, Senior Facilities Engineer, Plessey. “The Envirogen team took the time to understand our exact requirements. The ASTM standards we require exceed those for every other industry and it could be tempting to jump straight into a new installation, but Envirogen showed us how we could use our existing assets without compromising quality. We have accomplished everything we set out to achieve in a very challenging landscape, within a tight timeframe.”
“Once we’d signed the proposal, this was when the real work started,” continues James. “We were firmly within a lockdown situation when we signed the contract, but the ultra-pure water systems needed to be up and running by October 2020 if we were to hit our targets to commence manufacturing. The microLEDs that we are making for augmented reality are ground-breaking and there is no room for delay when you are working with next-generation, disruptive technology. Envirogen’s engineering team pulled every string to get to site while complying with the strict regulations. Special licences were awarded to allow the engineers to stay overnight and continue to work on upgrading the system.”
Updating every system without disrupting the flow
Each element of the ultra-pure water systems required refurbishment or upgrade, but current manufacturing processes couldn’t be stalled.
Bill Denyer, UK and European CEO at Envirogen Group, said:
“In essence, we needed to perform open-heart surgery on the live circulatory system that supplies the entire factory. This is always challenging, but we also had the additional pressure of maintaining stringent water quality standards throughout. We were working at the parts per billion (ppb) level for silica and total organic carbon (TOC) so just a minor change could have a big impact at this level.”
To maintain ASTM standards throughout the refurbishment, the team began work at the pre-treatment stage and worked its way downstream, gradually increasing quality standards on both the previously redundant and live systems. At every stage, potential bottlenecks were addressed to ensure that the 30m³ per hour flow of ultra-pure water was achieved.
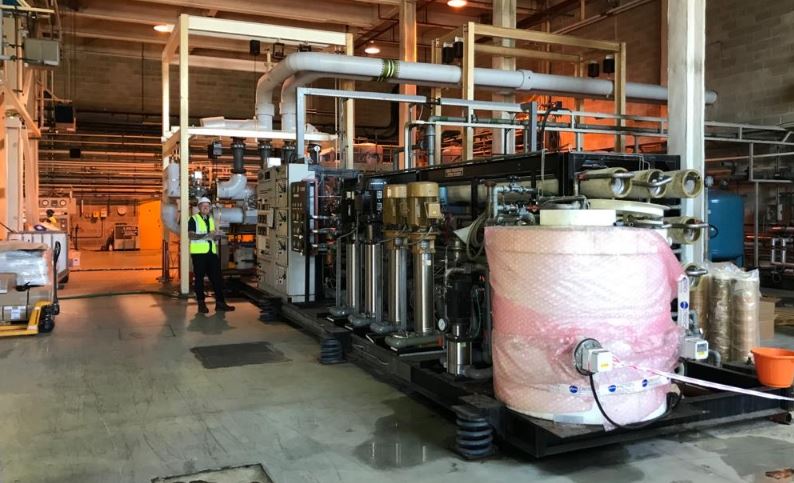
A staged refurbishment approach maintains ASTM standards for a live system
Stage 1: pre-treatment filtration
Incoming water is first passed through two existing multimedia filtration systems. These systems were upgraded and a third system added to provide the flow rate needed to feed downstream processes. The third system now supplies the same output as the previous two systems combined.
Stage 2: Reverse osmosis treatment
A triplex reverse osmosis system was reinstated on site. Membranes were replaced on the reverse osmosis systems already in use and a third unit was restored, rebuilt and connected to the other systems.
Stage 3: Roughing mix beds
New demineralisation media was installed for all four roughing mix beds. By matching the specific gravity and molecular weight of the individual beads in the original media, water standards were ensured. All diaphragm control valves, solenoid actuators and pneumatic lines were replaced to stop previously reported failures from occurring in the future.
Step 4: Polishing mix beds
The media was replaced in each of the four polishing mixed bed units. The resin was selected to provide ultra-low TOC levels and reach the very high resistivity levels required. Greater exchange capacity was achieved by increasing the volume in each vessel from 650 litres to 700 litres.
Step 5: TOC reduction system
A new ultraviolet (UV) unit was installed as a TOC reduction stage to replace a damaged unit. The unit was built to order and doubled the TOC reduction capacity from 18m³ per hour to 36m³ per hour.
Step 6: Final filtration treatment
Finally, new filters were installed in the existing 0.1-micron duplex, stainless steel, cartridge filter vessels and triplex 0.04-micron housings, a specificity unusual outside of electronics manufacturing. The filters ensure ultra-pure water standards at less than 1 ppb silica and less than 1 ppb TOC, half the amount previously achieved and well within the ASTM guidelines. High resistivity levels are protected at levels greater than 17.8 megaohms.
Step 7: Fabrication loop sanitisation
Once all the refurbishment and upgrade works were completed, a full chemical sanitisation of the refurbished fabrication loop was carried out to remove any debris, biofilm or bacteria that may have been present in the pipework. This was achieved by utilising the on-site clean-in-place (CIP) system already integrated into the water treatment plant and ensured the fabrication loop was in the best condition possible to receive the ultra-pure water.
Maintaining standards for years to come
Following the installation, Envirogen engineers continued to provide ongoing training and optimisation advice. Flexible coaching programmes meant that operators received relevant and practical on-site advice as they worked with the updated systems.
Plessey has also taken out an ongoing PureCare service and maintenance contract. Envirogen engineers regularly attend site to complete planned maintenance tasks and ensure that Plessey continues to achieve optimal efficiencies and high-quality, ultra-pure water standards.
Key outcomes
- Existing ultra-pure water systems upgraded, doubling output from 15m³ per hour to 30m³ per hour
- Redundant equipment upgraded to required specifications, generating over £1 million in savings versus a new installation
- System fully designed, installed and commissioned in just six months while working in Covid-19 lockdown conditions
- Full fabrication loop sanitisation ensured that the ultra-pure water specification could be delivered to the manufacturing lines as soon as the system was put live
- Process water now exceeds ASTM standards, including:
- Less than 1 ppb silica
- Less than 1 ppb TOC
- Greater than 17.8 megahms of resistance
- Ongoing PureCare service, maintenance and consumables plan ensures continued optimisation and efficiency of the ultra-pure water systems
- Ultra-pure water will be used to drive the groundbreaking manufacturing needed to realise next-generation technology.
For a free assessment to evaluate water treatment and process filtration solutions for your site, contact our team of expert engineers
About the client
Plessey is an award-winning embedded technologies developer at the forefront of emerging microLED technology for augmented and mixed reality (AR/MR) display applications through the combination of very high-density RGB pixel arrays with high-performance CMOS backplanes producing very high-brightness, low-power and high-frame-rate image sources.
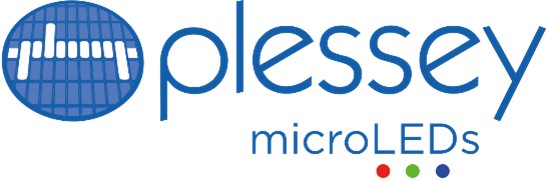