When the time came to replace an ageing ion exchange system feeding purified water to their paint shop, Honda approached Envirogen Group for a fresh perspective. Could they use this opportunity to increase safety standards on-site, as well as lower their water and energy usage to meet sustainability goals?
Reverse osmosis water treatment might just provide the answer.

The Honda factory produces and sells a quarter of a million cars a year throughout Europe. A key part of the production line is the multi-part paint process. This expensive, automated, robotic electroplating system requires a constant supply of purified water. The ion exchange filtration system that historically provided this water was approaching the end of its natural life and it was time to look at new options. Honda was keen to reduce water usage and make energy savings but needed to ensure that the complex water requirement could be met, in order to protect the electroplating system.
High pressure saves water and energy
Purified water is required in two main areas: to supply the paint ash process, which uses an acid treatment to provide a stable base for the paint to adhere, and to supply the paint dipping procedure, which uses electroplating to bind the paint to the surface of the car.
To avoid impacting the complex chemical and electrical processes, the water input must be treated to reduce its conductivity and remove impurities.
An ion exchange system can achieve these results but requires frequent regenerating using hydrochloric acid and caustic soda. With this comes the need for safe storage and handling of these chemicals and a requirement to neutralise the resulting effluent. With Honda’s framework for health and safety and risk reduction, the existing process was clearly an area under scrutiny.
“A reverse osmosis water treatment system was a clear winner for the team,” explains Bill Denyer, UK and European SEO, Envirogen Group. “For the paint dip part of the process, Honda required water conductivity of less than 10 micro siemens (µS). Although ion exchange systems can achieve this, reverse osmosis technology does so without the need for chemical recharging, removes the risk of chemical handling and doesn’t create a chemical effluent that requires neutralisation. By designing the reverse osmosis water treatment system with our high-quality membranes, we ensured a low total cost of ownership. The filters and reverse osmosis membranes last longer and perform better, saving water .”
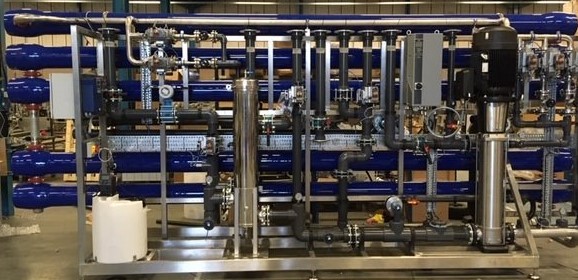
Reducing waste with the security of supply
The system takes incoming water directly from the town’s water supply and feeds it to three banks of reverse osmosis skids. The first supplies the cooling tower, which supplies the paint ash process and the second supplies the electroplating process. The third system provides a dual purpose. The water produced by the first two system recovers 75% of the water, which means that 25% containing the concentrated ions and other impurities are removed as a neutral waste stream. The third reverse osmosis skid takes this waste stream and reprocesses it, raising the recovery rate to 90% while still holding the salts in solution and allowing disposal to drain with no further effluent treatment required. This additional recovery will help Honda to continue to build year on year on its water efficiency targets.
The third reverse osmosis system is also used as a backup during planned maintenance and can be switched to take a direct supply of town water. This extra capacity means Honda can ensure a 24-hour operation to meet demand, even when treatment skids are being changed or the systems cleaned.
An additional ultraviolet (UV) sterilisation system screens the water for any colony forming units that might impact on the quality of the processes or the final paintwork.
The resulting purified water is held within purpose-built 30m³ and 25m³ storage tanks ready for use as and when needed. The entire plant has the ability to produce 75m³ per hour of purified, process-ready water.
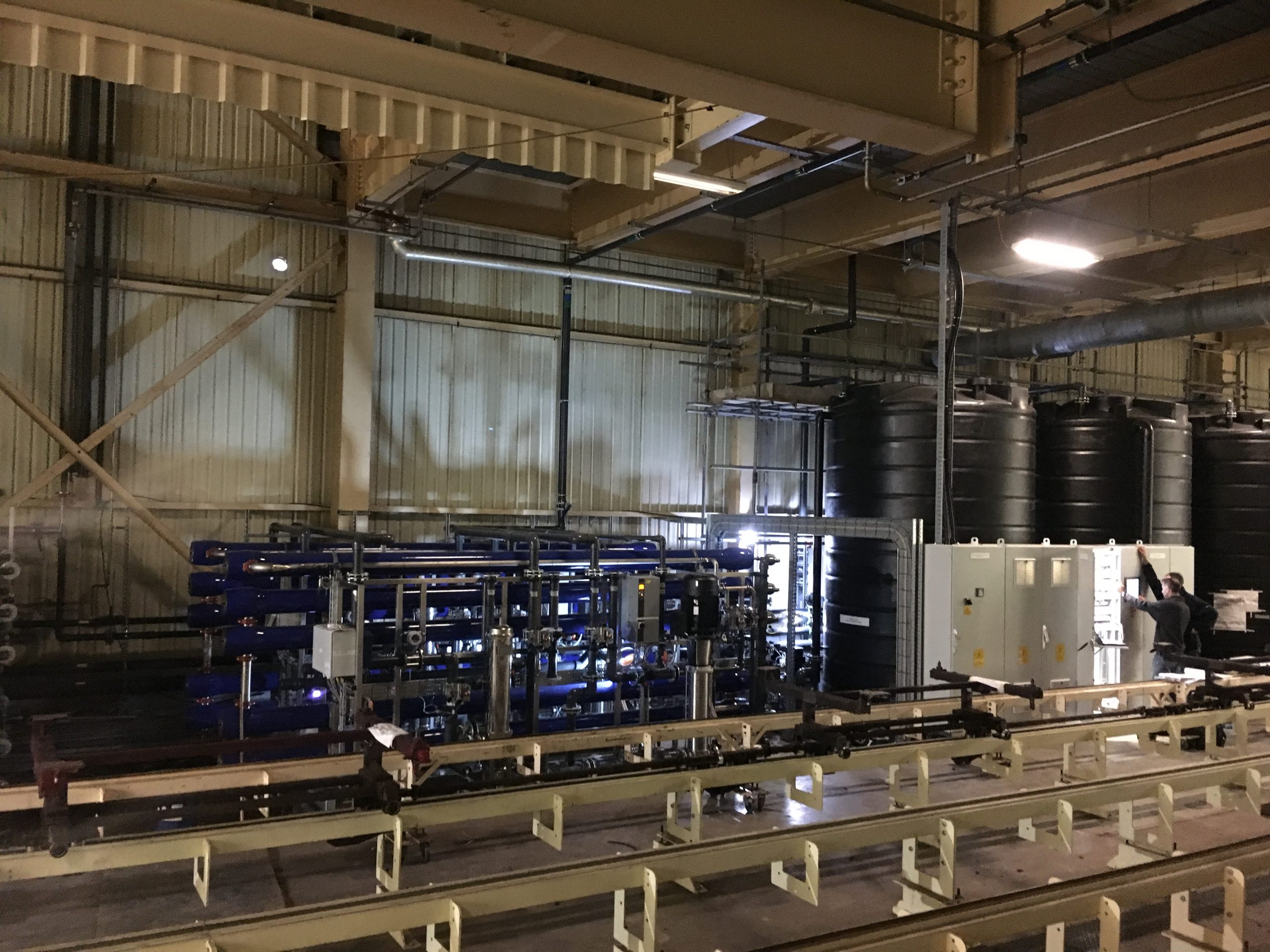
From signature to flow in just six months
“Honda chose us because of our innovative design, engineering knowledge and our full-service offering,” continues Denyer. “We have decades of experience working with industrial applications like this and we always design solutions to meet the exact needs of our clients in their bespoke process. No two systems are the same, but they often contain modularised aspects. By combining tried and tested modules within a bespoke design, we fulfil the requirements while achieving a low total cost of ownership and reduced initial capital outlay.
“We understand the demands in high-speed manufacturing and our clients can’t afford to waste time when moving to a new system. We installed and commissioned the system with minimal disruption to site ensuring there was no interruption to the manufacturing process.
“Our work with Honda didn’t stop when we installed the system. We also provide our ongoing PureCare Priority Response 24-hour service and maintenance contract. Honda has the peace of mind that their system will continue to run reliably to maximum efficiency, day after day. This package also includes key consumables, which we keep in stock so that the Honda site never has to wait, as well as monthly site visits and inspections.”
Key outcomes
• Full RO technology and UV sterilisation system with holding tanks to produce up to 75m³ of low conductivity water per hour.
• Operating cost savings compared to the previous ion exchange system.
• Chemical storage and handling are no longer required with this safer process that requires no chemical recharging.
• 90% water recovery rate achieved through the concentrate recovery system.
• Additional capacity ensures 24-hour flow, even during planning maintenance and cleaning.
• 24-hour service and maintenance contract, PureCare Priority Response, ensures the system runs to maximum efficiency, every day.
For a free assessment to evaluate water treatment and process filtration solutions for your site, contact our team of expert engineers
About the client
Established in 1948, Honda Motor Company Ltd is a Japanese car, motorcycle and power product manufacturer.
