Coca-Cola’s flagship manufacturing plant in Wakefield, UK, is the largest soft drinks plant by volume in Europe, owned and run by Coca-Cola European Partners (CCEP). When the previous process water treatment plant, supplying many of its manufacturing lines, began to reach the end of its life, the team started to evaluate the whole incoming water process. Envirogen Group was asked to design a system that would meet the needs of the site, but the new plant would achieve much more.
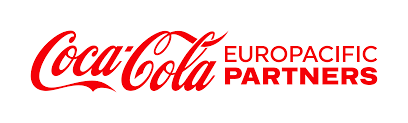
CCEP’s water requirements at Wakefield are complex and numerous. Supported by a focus on manufacturing excellence and a core strategy of producing soft drinks in a way that is as productive, efficient and sustainable as possible, the site has evolved since opening its doors in 1986. For this reason, different lines have different requirements, depending on the products that they make and the age of the systems that power them. Newer lines are built to a continuous manufacturing specification, mixing syrup and purified water seconds before the bottle or can is filled and sealed, whereas older lines work on a batch process using holding tanks.
Thanks to successful installations at other CCEP sites, combined with the team’s comprehensive design, installation, engineering and project management experience, Envirogen won the contract. The completely new process water treatment plant system would be designed and constructed to feed all factory lines.
Future-proofing with flexible systems
The factory requires process water of two different specifications, a high standard of purified water to feed all lines and an additional deoxygenation stage for batch manufacturing. This additional stage ensures that water can be stored without impacting the taste of the end product while providing greater control at the carbonation phase of production.
Envirogen designed and built the entire new water processing plant, consisting of a stainless-steel semi-treated tank, a triplex pump to forward the water to pump skids which feeds into a central UV sterilisation system. This process water is then forwarded straight into the continuous processing line, with the water required for the older batch processes fed into an additional treatment stage.
“An existing degas strip tower was deoxygenating the treated water, but this is an outdated piece of equipment” explains Bill Denyer, UK and European CEO, Envirogen Group. “It’s bulky and constrained to a set volume, so it isn’t future-proofed. With the freedom CCEP gave us to design an optimal system for their requirements, we were able to create a much smaller system that can adapt to the needs of the site.”
“This future-proofed system consists of a nucleus of hydrophobic membranes to liberate the oxygen instead of the large degas strip tower. The system has been designed for the requirements of the site as it is but, if a higher specification of water or a higher volume is required, more membranes can easily be added in series or in parallel. The old degas strip tower was limited to a set volume. This new system takes up a much smaller footprint but allows the system to flex with the requirements of the manufacturing lines.”
“This new online system works at low pressure, meaning that additional power-hungry pumps are not required, and energy consumption and operating costs are lowered.”
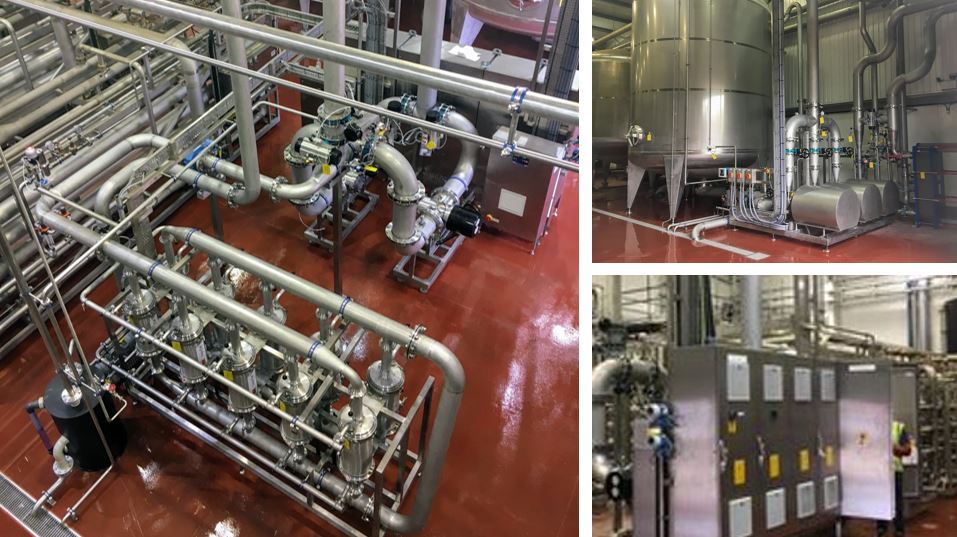
From 3D imaging to ongoing care
In order to help CCEP visualise the new plant, the room was scanned, 3D models of the whole water treatment plant room were created to give an overall picture of its spatial arrangement. The team could drill down into every detail, with every pipe, connector and tank specified.
The new treatment plant was manufactured at Envirogen’s world-class manufacturing centre in Alfreton, UK to Coca-Cola’s own KORE standards. The KORE specifications include some of the most rigorous product safety, quality, health and safety and environmental regulations in the industry. The system was built to comply with each and every one of these rules, from engineering and electricity specifications right down to the tags attached to each pipe.
During planned weekend shutdowns, parts of the new system were switched on and commissioned in stages. Final user acceptance and water quality tests confirmed that the system was producing process water to the pre-defined KORE standards.
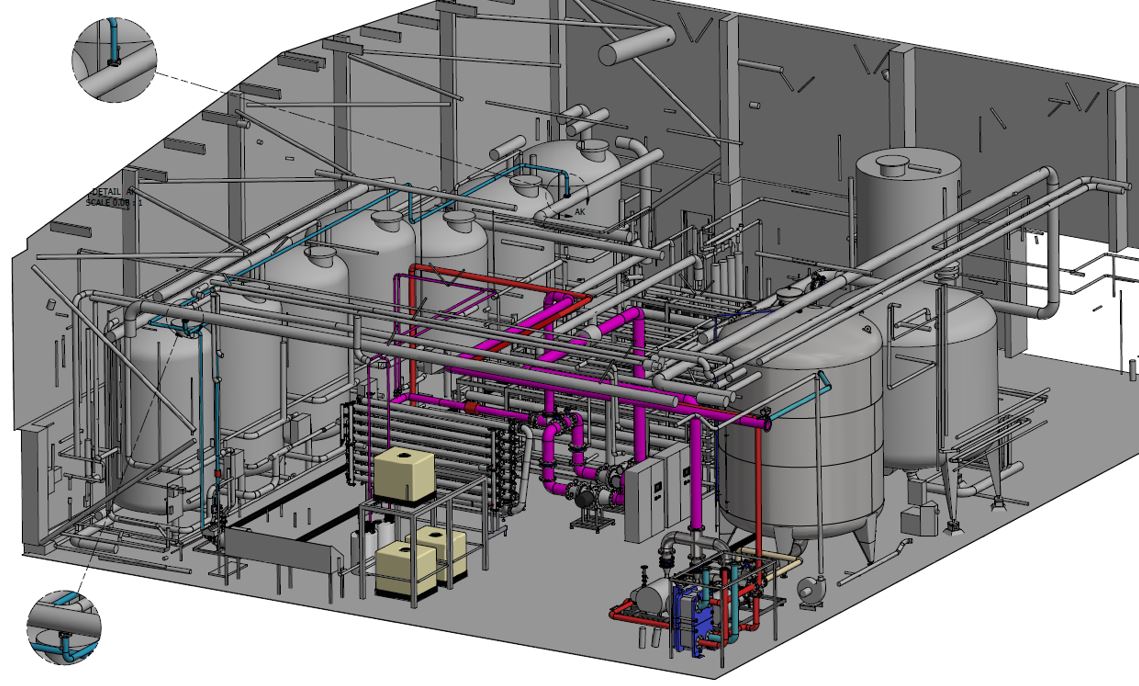
“Our work didn’t stop there,” continues Denyer. “CCEP also signed up to our PureCare service and maintenance contract to ensure that the system continues to work at maximum efficiency for as long as possible.”
“Envirogen’s team of expert, local engineers attend the site regularly to replace consumables and carry out comprehensive preventative maintenance, giving advice to operators to get the best out of the system.”
“Following the success of the Wakefield project, we have worked with other CCEP factories around Europe and the team continues to upgrade systems to achieve even greater efficiencies, cost savings and reduced environmental impact for the brand.”
Read more about our process water work at another CCEP factory in Edmonton.
Key outcomes
• New process water treatment plant provides two different specifications of water to feed differing manufacturing processes.
• Hydrophobic membranes replace stripping tower, reducing footprint and future-proofing the plant for change or expansion.
• Entire water processing plant commissioned during planned weekend shutdowns with zero impact on factory output.
• Compliance with Coca-Cola’s exacting KORE standards, delivering manufacturing excellence through productively, efficiency and sustainability.
• Ongoing service and maintenance plan ensures the new process water treatment system delivers maximum efficiencies and return on investment.
For a free assessment to evaluate water treatment and process filtration solutions for your site, contact our team of expert engineers
About the client
CCEP is the largest Coca-Cola bottler by revenue, with over 23,000 employees working in 13 Western-European markets. CCEP makes, sells and distributes some of the world’s best-loved drinks to millions of customers and consumers.
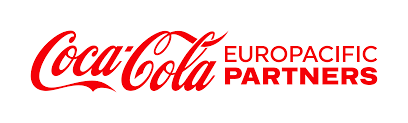