When the reverse osmosis (RO) plant supplying the endoscope reprocessing unit at Good Hope Hospital, part of University Hospitals Birmingham NHS Foundation Trust (UHB), began to produce poor total viable count (TVC) results and with the existing plant becoming difficult to repair, UHB faced the dilemma of requiring a permanent replacement unit, while needing to maintain the endoscopy service for its patients with a temporary reverse osmosis hire unit.
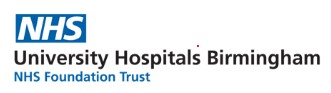
Sharon Fox, head of decontamination central endoscopy decontamination units and sterile services at UHB, explains: “It was simply not an option to shut the endoscopy department down, as we needed to continue to provide a high-quality service for our patients. We also did not want to reprocess the endoscopes off-site. We were trying to find a solution, when it was suggested that we could take one of the washer-disinfectors out of service and put a temporary RO unit in its place.”
Envirogen Group, the RO manufacturer chosen for the project following an extensive selection process by the estates department, had a reverse osmosis hire unit available. One of the endoscopy department’s washer-disinfectors was disconnected and the rental unit installed in front of it. “We couldn’t have positioned the RO unit any closer,” says Sharon. “We had no service issues whatsoever, which was fantastic.”
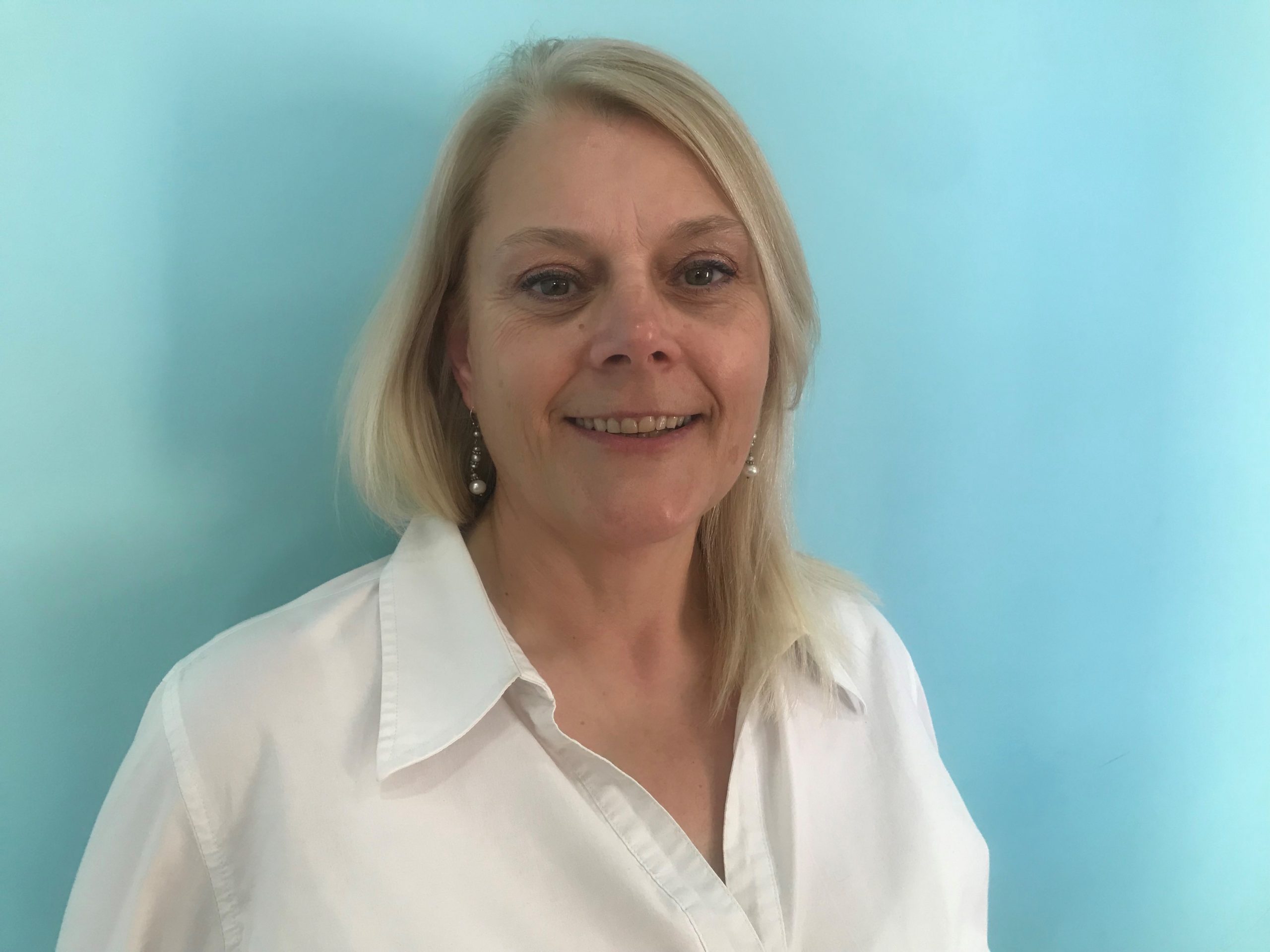
Sharon Fox, head of decontamination, central endoscopy decontamination units and sterile services, University Hospitals Birmingham NHS Foundation Trust
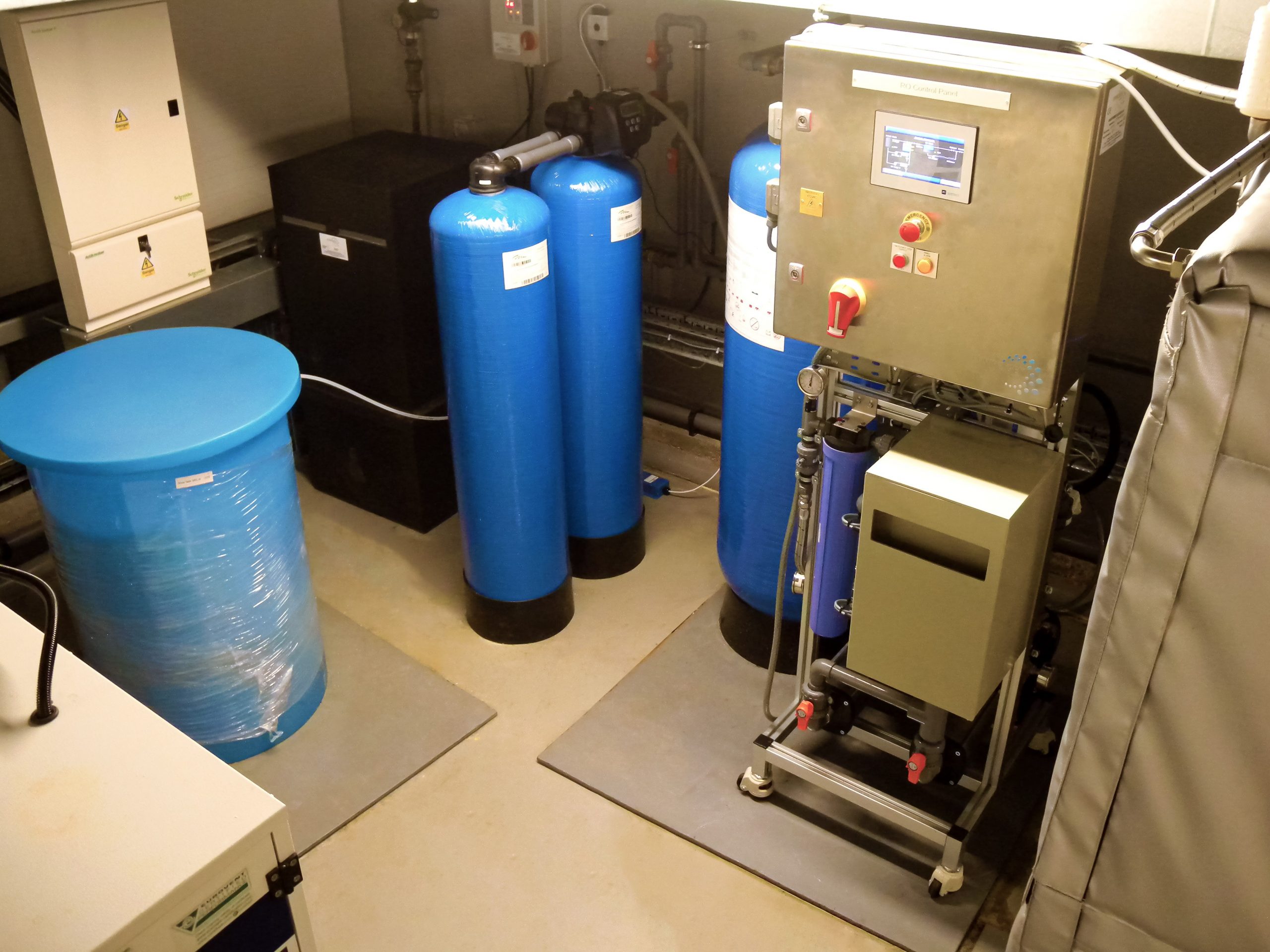
The Envirogen EndoTherm Duo Modular skid-mounted duplex RO system provides 100 per cent resilience
Outlining the role of the UHB’s estates team, recently appointed estates manager, Neil Turnbull, explains: “When I came into post, the selection process for the replacement RO had already been completed. Estates ordered the rental unit and were involved in some enabling works. We checked the size of the existing water tanks, which were already in the plant room. The water and electrical supply were increased accordingly. A structural engineer checked the spread load.”
As soon as the reverse osmosis hire unit was commissioned and signed-off, work began to replace the old RO unit and install the permanent replacement system. To ensure everything ran smoothly, weekly online meetings where held throughout the project, involving estates, the endoscopy and decontamination team and Envirogen.
Sharon says: “The plant room is quite some distance from endoscopy. Envirogen advised that the existing plastic pipework and diameter was not suitable for the scheme. So, the old pipework was removed and replaced with a larger diameter stainless steel ring main.
“The installation went smoothly. All the commissioning and mycobacterial tests passed with a ‘clean bill of health’, which was really good.”
On the advice of the RO manufacturer, the endoscopy department retained the RO water treatment rental equipment in position on site for a month, to ensure that everything was running smoothly, before it was finally removed.
Sharon adds: “The department has now been operating for almost a year with no service issues whatsoever. The new RO unit is remotely monitored and can be adjusted if required with the manufacturer making us aware, if necessary.
Wayne Spencer, UHB’s authorising engineer (decontamination), says:
“Replacing key pieces of equipment in a busy department is always a challenge, especially so when space is limited. The project required the department to use their endoscope washer-disinfector capacity for extended time periods, due to the temporary rental RO plant being in place.
Describing the RO system and installation in detail, Allan Wigglesworth, Envirogen Group’s healthcare market manager, says: “The system is from our EndoTherm Duo Modular product range, a compact duplex RO unit, sized to serve the six or eight endoscope washer-disinfectors which the hospital planned to install as part of its development programme.”
Designed for endoscopy and sterile service applications, the EndoTherm Duo Modular range of RO systems meets the water quality standards of HTM01-06, HTM01-01, ISO15883 and AS/NZ 4187.
The units can be set to operate at ambient or elevated temperatures and are user adjustable. Automatic thermal sanitisation takes place out of hours. All models can be either electric or steam heated. The units use a combination of reverse osmosis, ultra-violet disinfection, sub-micron endotoxin filtration and constant recirculation, which all work together to maintain good water quality. The range of dispense rates can be matched to single or multiple decontamination equipment needs.
A full colour touch screen HMI monitor allows for secure access levels, simple maintenance procedures and displays real-time graphical data. The compact, pre-assembled, skid-mounted EndoTherm Duo Modular units are fast and easy to install, commission and validate.
“The top floor plant room is some distance from the endoscope reprocessing unit and required about 180 metres of orbitally welded stainless-steel pipework to feed the RO water,” explains Allan. “The previous installation had used a narrow PEXa ring main, which is usually associated with renal dialysis installations. We removed this and installed a new, larger, one-and-a-half-inch stainless steel pipework system. To avoid the disruption of the pipework running inside the consulting and treatment rooms, the new ring main runs partly outside the building and is fitted with protective trace heating.”
Allan says: “Within the reprocessing unit, the ring main has a stainless-steel header in a removeable manifold with tri-clamp fittings. It’s a sanitary method of connecting stainless steel pipework without welding. This sits above the current washer-disinfectors. It will enable the ring main to be easily disconnected from the machines when these come to be replaced in the future, prior to fitting a new manifold and connecting the RO to the new washers. This will ensure that there is minimal downtime or revalidation required for the RO water system when the machines are installed.
“When the new equipment was manufactured and delivered to site ready for installation, we commissioned and validated one of our reverse osmosis hire units in the endoscope reprocessing department. This enabled the service delivery to continue uninterrupted while the scheme went ahead. The rental unit was a small EndoTherm Mini system, sized to supply the endoscope washers. It was installed in the reprocessing department, in front of one of the machines. This enabled the service to continue using the three available washer-disinfectors using a short, temporary ring main.
“The rental unit ran for nearly ten weeks, while the replacement RO unit was installed, commissioned and mycobacterial results validated. We then switched the washer RO feed over to the new EndoTherm plant. However, we suggested that the hire unit should stay in place for a month, whilst we ensured that the team were happy with the new equipment, training had been provided and that everything was running smoothly.”
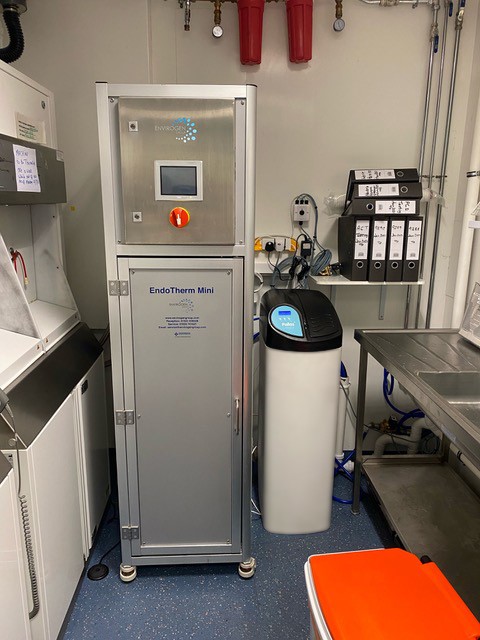
An Envirogen EndoTherm Mini reverse osmosis hire unit enabled the department to maintain service while the scheme was completed
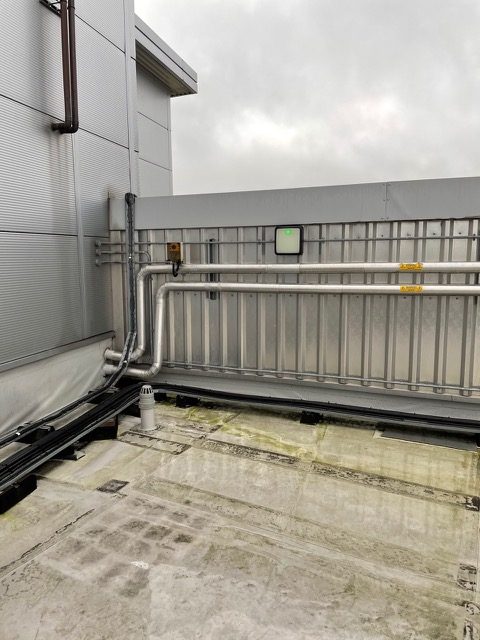
The extensive stainless steel ring main runs 180m from the plant room to the endoscope reprocessing unit
Allan adds: “The scheme was safely completed during COVID-19 restrictions. It was delivered through NHS Supply Chain, a normal procurement route for us. It is covered by a two-year warranty, with the reassurance of including all parts and call outs. The installation features a remote digital monitoring programme enabling our service centre to dial in remotely and make various adjustments without visiting site.
“Being a duplex system with 100 per cent resilience, we can work on one RO unit and change filters or pumps, for example, while the other unit has full capacity without the need to shut down the ring main. The main elements of the system are manufactured and tested at our UK facility in Alfreton, Derbyshire, where factory acceptance testing is available.”
While chosen following a three-way selection process for the scheme at Good Hope Hospital, Envirogen is no stranger to UHB. An Envirogen duplex RO system serves the main endoscopy unit at Heartlands Hospital, where a mobile endoscopy unit also features another of the company’s machines. Another EndoTherm duplex RO unit is also installed at Solihull Hospital.
About the client
Good Hope Hospital, part of University Hospitals Birmingham NHS Foundation Trust (UHB), serves North Birmingham, Sutton Coldfield and a large part of south-east Staffordshire, including Burntwood, Lichfield and Tamworth. The catchment population is about 450,000.
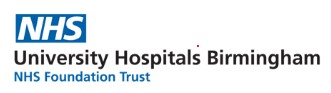
For a free assessment to evaluate water treatment and process filtration solutions for your site, contact our team of expert engineers