Growing patient numbers and rising demand for reliable endoscopy services meant that the hospital needed to review its key reprocessing equipment. This resulted in a recommendation that their existing chemical clean reverse osmosis units be replaced with state of the art thermal sanitisation reverse osmosis (RO) systems.
Its existing chemical clean RO units had routinely failed on water quality rendering the Automated Endoscope Reprocessors (AERs) it fed being taken out of service.
Envirogen Group was selected following a competitive tender process through the NHS Supply Chain, where all tenders were provided a design specification and an opportunity to visit and survey the site.
Designed for compliance and peace of mind
A key requirement was the need for n+1 duplex design for maximum resilience. Twin EndoTherm Mini reverse osmosis units were put forward by Envirogen as the most viable solution, each feeding its own stainless steel distribution ring main. Each ring main was to feed three Automated Endoscope Reprocessors (AERs) chambers.
Additionally, the hospital confirmed there were to be no single points of failure and as such supplying two duplicate systems was the only compliant design so that in the event of one reverse osmosis (RO) system being serviced/repaired, the second would assume full duty to all AERs.
Allan Wigglesworth, Healthcare Market Manager, Envirogen Group, explains:
“This n+1 design is one we use quite often as it provides maximum resilience. The EndoTherm Mini is a proven system with many installations up and down the country. The automated thermal sanitisation function, programmed to run out of hours means an end to the handling, use, storage and purchasing of expensive hazardous chemicals.”
“We recommended a duplex design for non-stop, resilient 24-hour endoscopy service. Each EndoTherm Mini works independently of the other but is capable of supplying all washers. This ensures that when planned maintenance work is needed, there’s still plenty of water to enable all AERs to work at full capacity. We also supplied a powerful HMI display with secure PIN access ensuring up to the minute reporting whilst key settings are protected.”
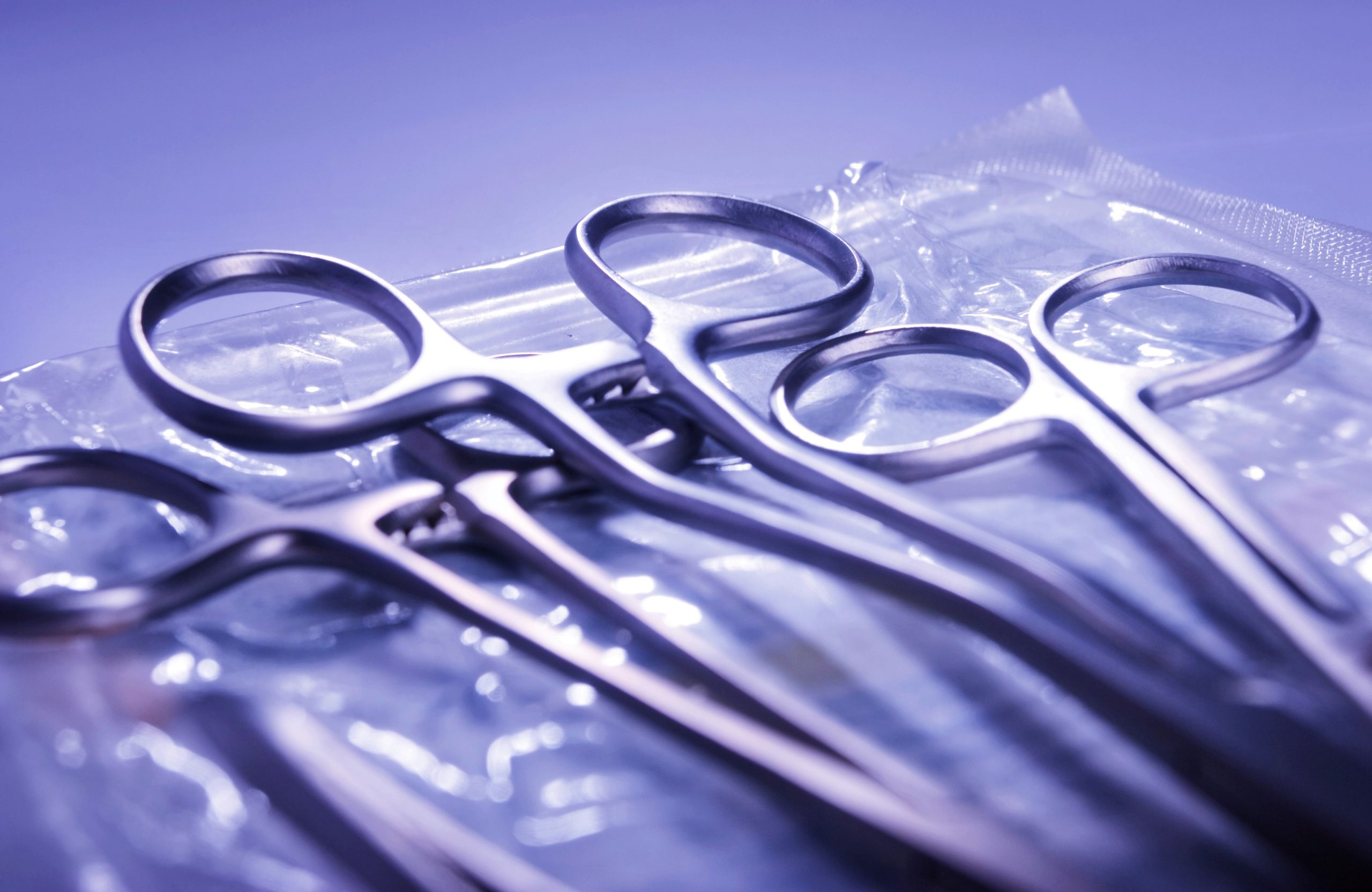
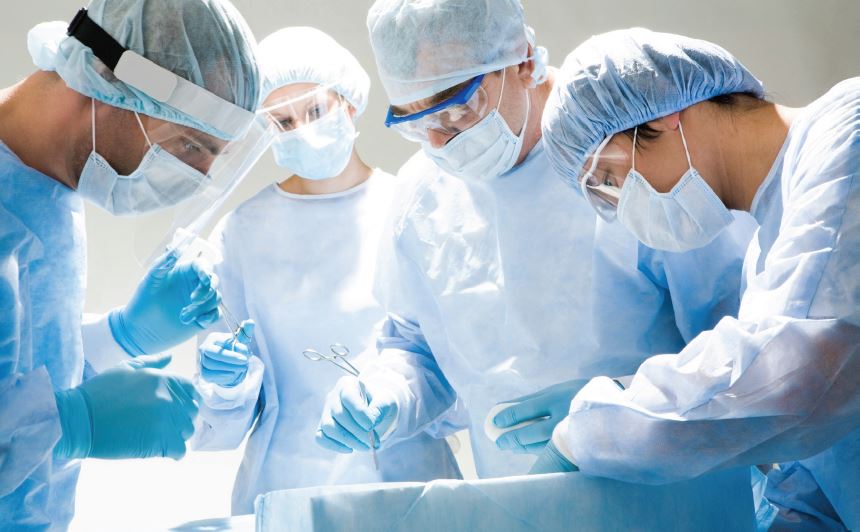
Installed to compact space, with zero downtime
An added complication was the fact that the RO units and associated pre-treatment equipment were to remain in an undercroft plant room (restricted height and access) directly below the endoscopy service wash room.
The design brief meant that the new RO plants were to be installed with zero downtime to the department. Not a single day of scope cleaning was to be lost. A dedicated project team from Envirogen worked alongside the hospital to ensure all services required were available in the right place, at the right time, prior to installation. By putting in and validating one new RO system first, full reprocessing duty was maintained at all times.
Installation takes place through four steps:
- Installed new 1” outside diameter orbitally welded stainless steel ring mains
- First EndoTherm Mini commissioned, validated, approved.
- Second EndoTherm Mini installed, validated, approved
- Once approved, old units and equipment removed and safely disposed
Futureproofed for expansion
Although the existing AERs were not being replaced as part of this project, they’re due for replacement at a later date. The Envirogen solution has been futureproofed so that it can easily accommodate an upgrade in endoscopy service output. The ring main system can be easily modified to suit any new AER outlet positions and is achieved by placing sanitary tri-clover connections at strategic positions within the stainless-steel ring main. The result is that any future adjustment is simple and the work can be completed with minimal downtime and expense.
The hospital was pleased with the installation, commenting that:
“The Envirogen Group lead the field in reverse osmosis technology, with long term reference sites and have real expertise in the healthcare sector. The duplex EndoTherm Mini gives us exactly what we need, when we need it. The installation was carried out with such professionalism that our department never missed a single day reprocessing scopes. We were so impressed that we’ve since purchased another for a satellite scope washer in a different part of the hospital.”
Key outcomes
- Endoscopy services unit can now reprocess many more endoscopes in a day
- No downtime associated with poor RO water quality
- Switching from chemical to thermal sanitisation saves the department time and money and minimises disruption as the sanitisation process takes place out of working hours
- Futureproofed solution to easily accommodate an upgrade in output
- Other areas of the hospital are now using the same equipment such is the success of this installation
For a free assessment to evaluate water treatment and process filtration solutions for your site, contact our team of expert engineers