Eco Park Surrey is in its final stages of commissioning as it prepares to come online to transform kitchen and refuse waste into electricity. This pioneering Energy from Waste (EfW) power plant will take 40,000 tonnes of food waste and 55,000 tonnes of general refuse waste a year and use anaerobic digestion and gasification to generate renewable electricity. Central to the working of this combined heat and power (CHP) plant is a steady stream of purified, demineralised water created through the latest reverse osmosis and electrodeionization system technology. This purified water stream protects the boilers and steam turbine, decreasing costs and increasing the water treatment plant efficiency.
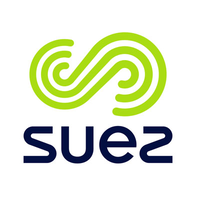
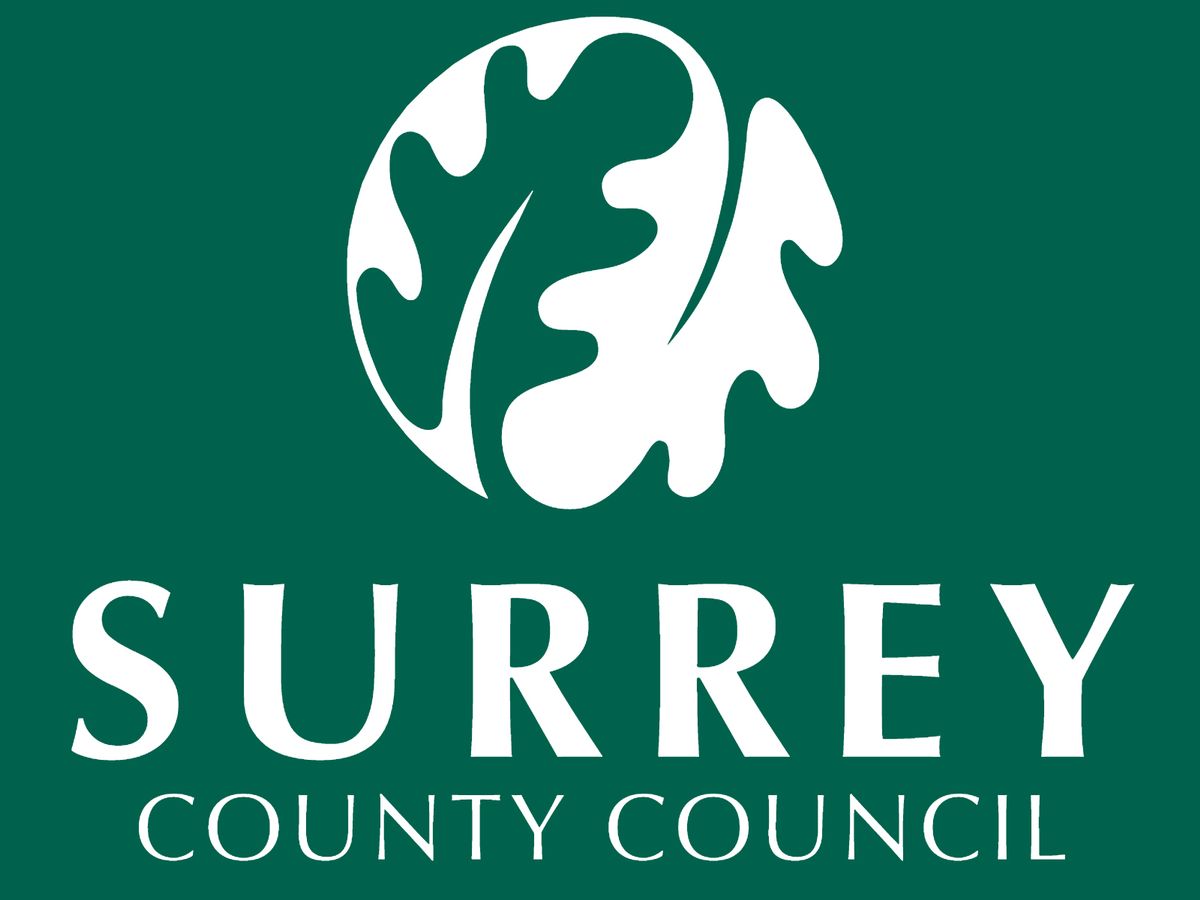
Purified protection
“The waste-to-energy market is growing and governments all over the world are looking for novel ways to meet the energy demands of growing populations. Plants like Eco Park Surrey are hugely important as they use the problem of landfill waste to fill the energy demand,” explains Ian Pearson, European Operations Director at Envirogen Group.
“Suez Recycling and Recovery Surrey is building the Eco Park on behalf of Surrey County Council. Suez is a major player in the power industry and an expert in creating and managing CHP plants. We were pleased to collaborate with them to provide the engineering know-how, technology and skills that they needed for the process water requirements.”
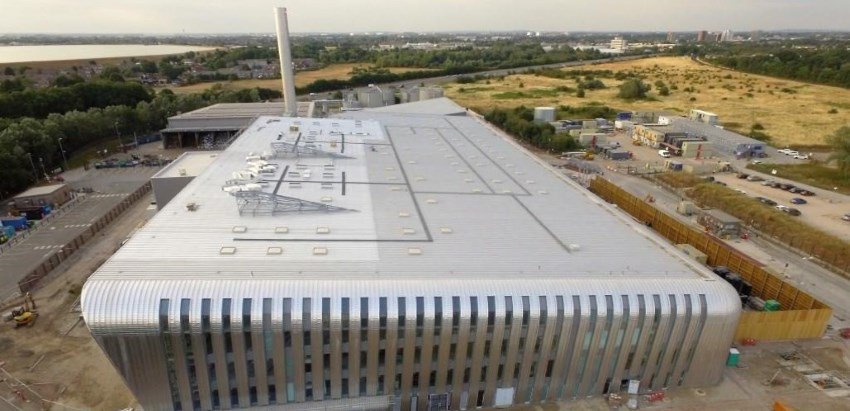
The Eco Park in Shepperton Surrey is a complete recycling and waste processing site, managed by Suez as part of a 25-year deal with Surrey County Council. Key elements of the wider site development include an anaerobic digestion plant that will convert kitchen waste into biogas and a gasification plant that will burn non-recyclable refuse. The gas from both systems will be burnt to heat water to steam that will, in turn, drive generators to produce electricity. This electricity will be fed directly to the grid, supplying renewable power to homes and businesses throughout the region.
“Demineralised water is needed to generate steam and this is where Envirogen comes in,” continues Pearson. “Although the steam cycle is designed as a closed system, modern boilers still require a stream of demineralised water to make up for losses. We designed a skid-mounted, combination reverse osmosis and electrodeionization system (RO-EDI) that delivers optimal performance, with low operating costs in the smallest possible footprint.
“Heating water is an energy-intensive process and scale formation makes steam generation processes less efficient. We’ve developed an automated boiler water treatment system that protects equipment and requires limited operator invention. Its design is perfectly suited to use in power plants and ensures a low operating cost.”
Three-step skid technology cuts operating costs
Envirogen recommended an all-in-one, multi-technology, RO-EDI plant system. This automated, integrated skid-mounted boiler water treatment system that includes the very latest RO-EDI water system technology. The three-step treatment uses reverse osmosis (RO) technology followed by gas transfer membranes (GTM) and finally electrodeionization system treatment to remove all scale-forming ions that might impact the efficiency of the generator. The resulting EDI purified water has a conductivity of less than 0.1 micro siemens (µS), with less than 10 parts per billion (ppb) silica and less than 3 ppb sodium.
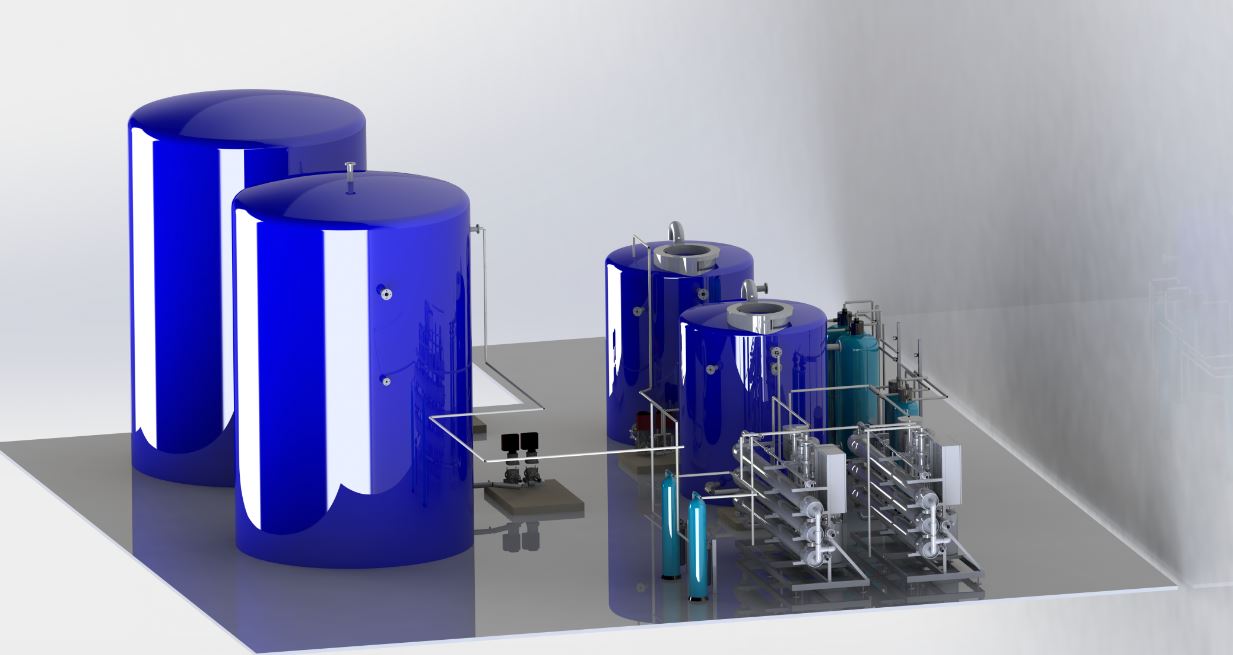
3D model designed to show the final electrodeionization system installed at the Eco Park
“This solution makes use of the very latest water purification technology,” explains Pearson. “Traditionally, resin beds would be used in a batch process to strip out the scale-forming ions. This is a complex operator-intensive process that involves equipment downtime. It also carries an added risk as the resin beds need to be chemically regenerated. This means chemical handling on-site and the generation of an effluent stream that needs to be treated. In a site that is completely focused on reducing waste and doing so in a safe and controlled manner, this wasn’t an option.
“The EDI system water treatment, requires no regeneration chemicals, using electricity to do this job instead. As only a small amount of electricity is required to perform the regeneration, the water treatment plant efficiency is maximised for little cost impact.
“Envirogen’s low operating cost philosophy is integral to its total solutions approach. Process filtration components are sometimes overlooked when clients look at a design, but they are often critical to the water treatment plant’s success. We select consumables that are designed to last longer and perform better than competitor systems; this means that RO membranes need replacing less often and this delivers operational and cost savings.
“Our modular, skid-based Eco MultiPro system is easily transferable to other energy applications, whatever the fuel. We’ve put considerable research and development investment into this design and by creating a modular system that is proven and tested in multiple settings, reducing costs for our clients. Our modular systems are effective solutions that have lower capital outlays and ensure low operating costs.”
Adding value through expertise and service
As incoming water varies by source and by region, Envirogen conducted detailed studies on the towns water supplying the boiler. A bespoke pre-treatment system was designed based on granular activated carbon (GAC) filters and softener resins.
Envirogen also provided additional waste treatment systems for the anaerobic digestor, removing solids and pH correcting for safe discharge.
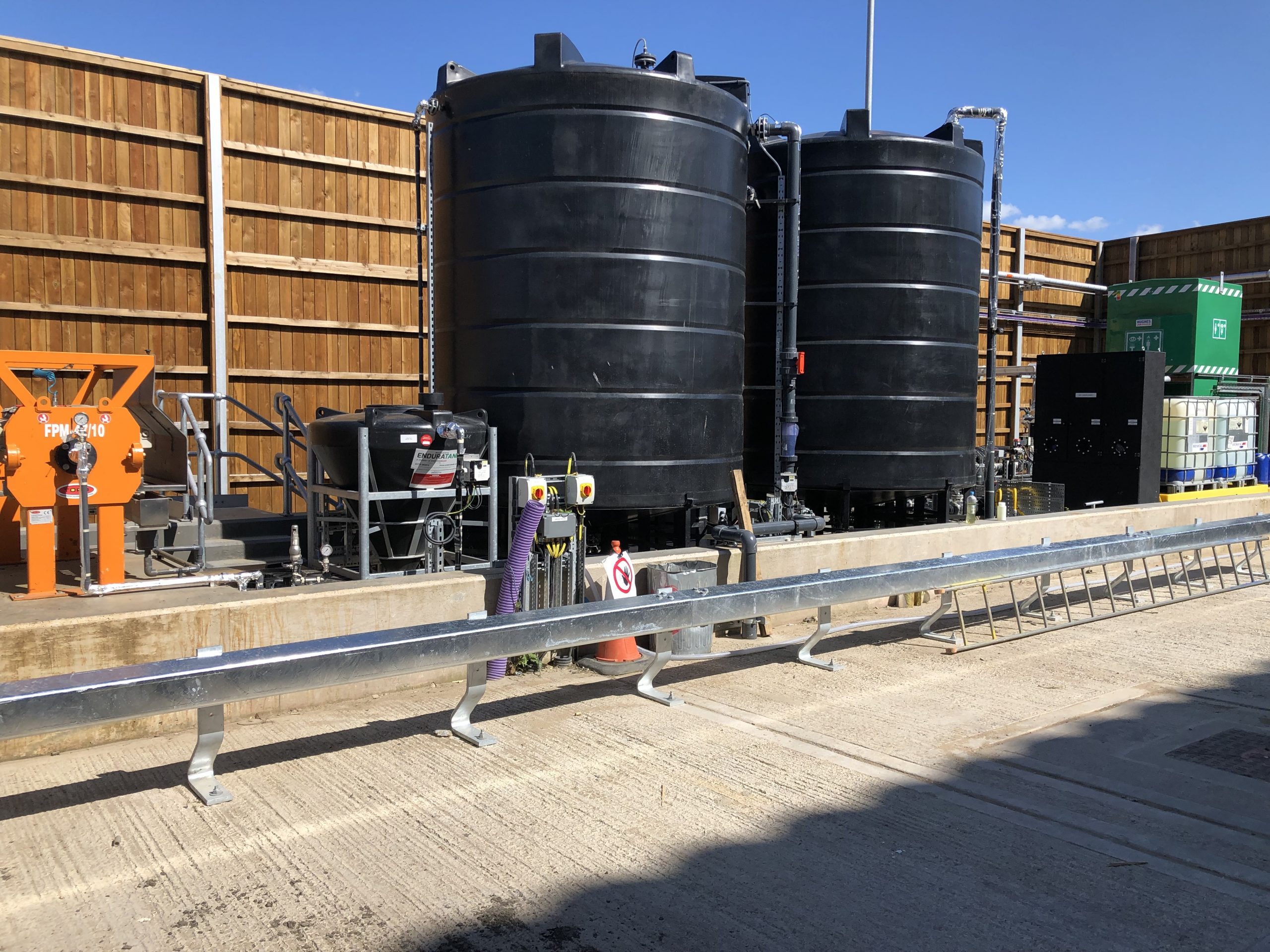
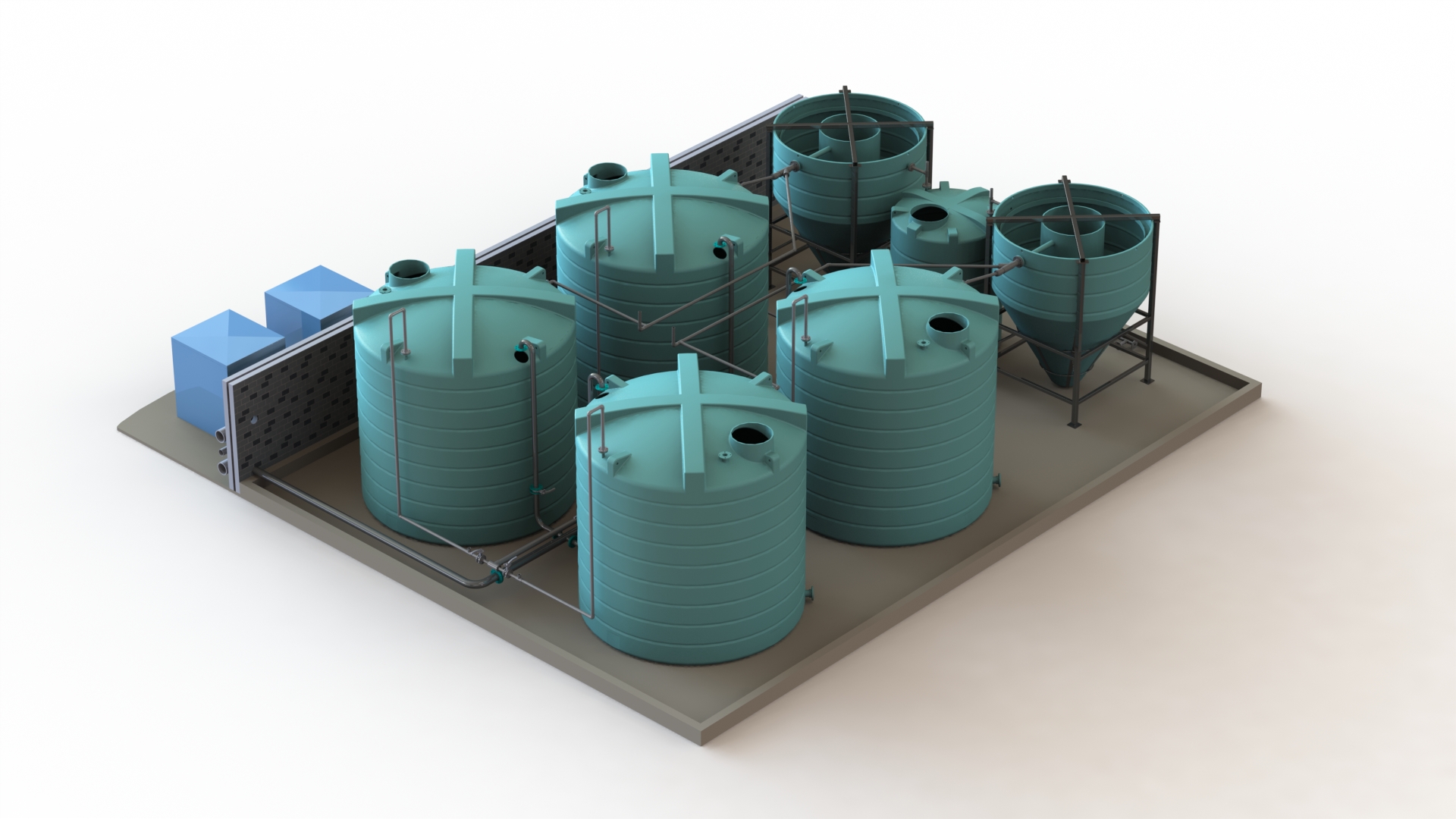
Ian Pearson, European Operations Director at Envirogen Group, said:
“All sites of this scale require multi-stakeholder engagement and involvement. We worked with the engineering consultancy appointed to design and build the Eco Park and with the end client. Being responsible for the installation and commissioning of the plant, we needed to drive coordination with the other contractors on-site, both to maintain the schedule and minimise the impact on other workstreams. In all large projects, we prioritise adding value to all stakeholder groups. We provide the specialist water treatment expertise and leverage this knowledge to support the project in its entirety, being proactive to recommend improvements that benefit the project as a whole.”
Eco Park Surrey is undergoing final testing and commissioning but will soon be fully operational. The anaerobic digestion facility alone has already generated 2.5GWh of electricity from 11,000 tonnes of food waste, enough energy to power 700 homes for a year. The gasification plant will have the capacity to power 4,262 homes when fully operational and can process up to 55,000 tonnes of black bag waste from three districts in north Surrey to generate electricity.
Interested in other power plant water treatment process projects?
For more information on other water treatment and process filtration solutions for the power and energy industry:
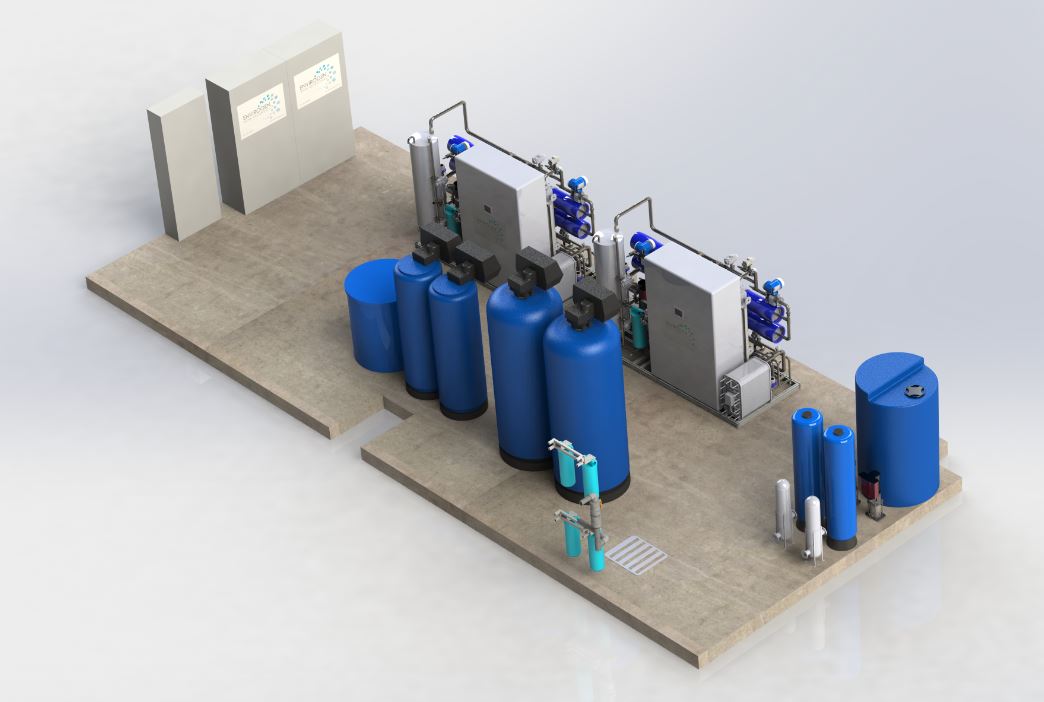
Discover how purified demin water helps Energy Works Hull generate enough energy from waste to power 47,000 homes.
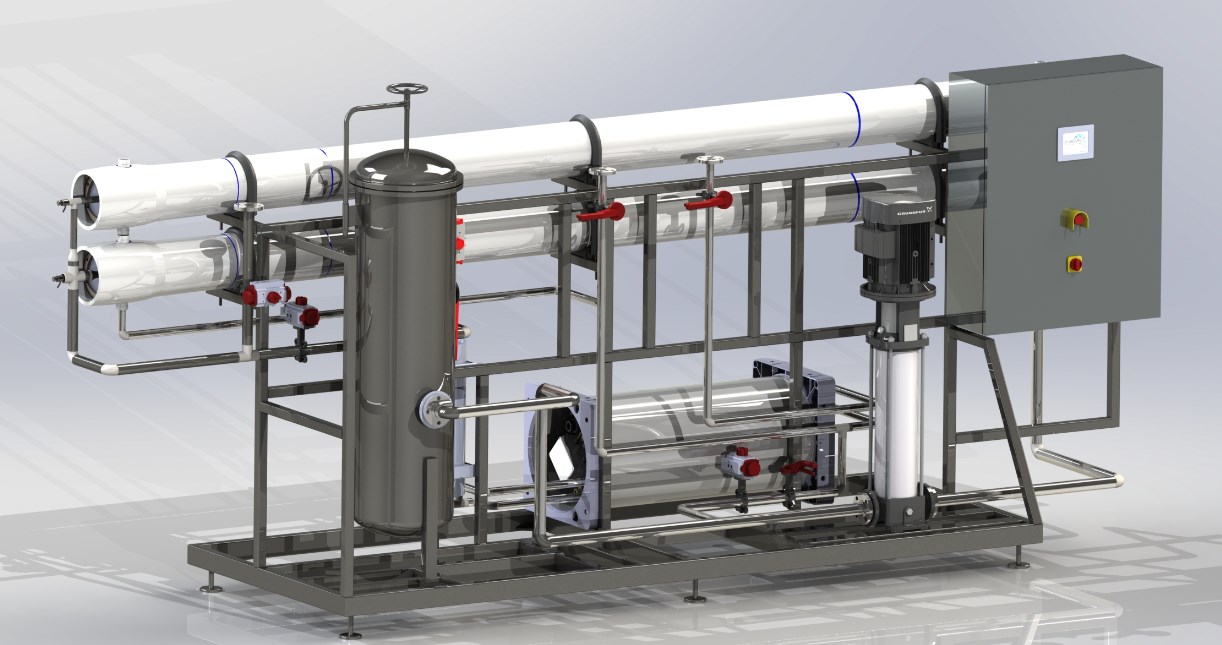
Key outcomes
- A complete skid-based demineralisation system installed to produce EDI purified water at a rate of 2 m³/hr.
- Modular, future-proofed design for flexibility and scalability
- A solution that meets the needs of a large and diverse group of stakeholders
- Process water conductivity reduced to less than 0.1 micro siemens (µS)
- With optimised water treatment plant efficiency, operating costs are reduced
- The latest electrodeionization system technology installed with no chemical treatment required
- Free electricity generated on-site is used to recharge membranes
- Anaerobic digestor waste stream treated to remove solids and neutralise pH for safe discharge
- Multi-stakeholder engagement and specialist water treatment support provided throughout the project in collaboration with engineering consultancy groups.
For a free assessment to evaluate water treatment and process filtration solutions for your site, contact our team of expert engineers
About the client
Eco Park Surrey is an initiative for Surrey County Council at Charlton Lane, Shepperton, UK. This collection of facilities will process waste from Surrey households to create fuel to power the National Grid and produce a soil improver, which can be used by farmers.
Suez Recycling and Recovery Surrey (previously known as SITA Surrey) is helping Surrey County Council move from a linear to a circular model in regards, to waste and recycling.
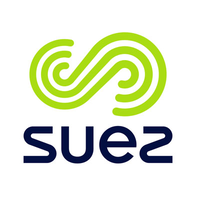
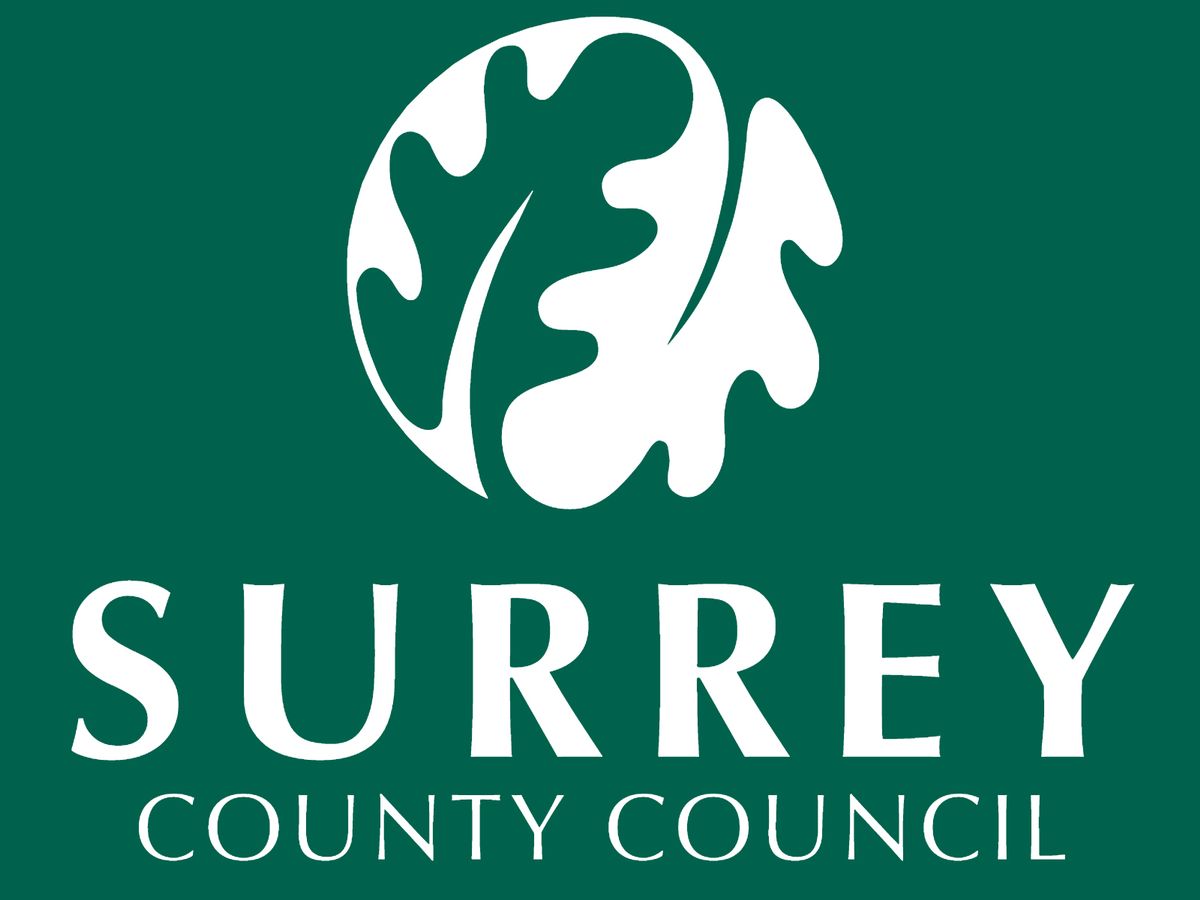