Investing in new filtration technology was the key to improving operations at Heineken’s Herefordshire cider mill. An old module was coming to the end of its life but instead of looking for a replacement, Heineken started to investigate the latest technologies. PureFlow crossflow microfiltration technology from Envirogen would come out clear winner.
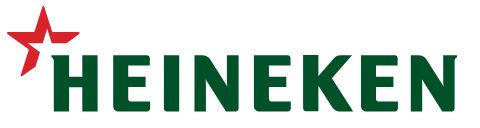
“We were impressed at Heineken’s advanced approach to improving efficiencies in their manufacturing centres,’ explains Bill Denyer, European CEO at Envirogen Group. ‘They were very open to exploring new technologies to maintain their high product standards, whilst looking to increase product yield and decrease operating costs.”
“The Herefordshire mill was operating ‘outside to in’ filtration technology, with air scouring back pulses used to regenerate the membranes. Although historically a reliable technology, it is liable to clogging and blocking, which has an impact on production timescales. Heineken were aware of crossflow microfiltration technology and when comparing the Envirogen PureFlow cider filtration model against competitor brands, it came out as the clear winner.”
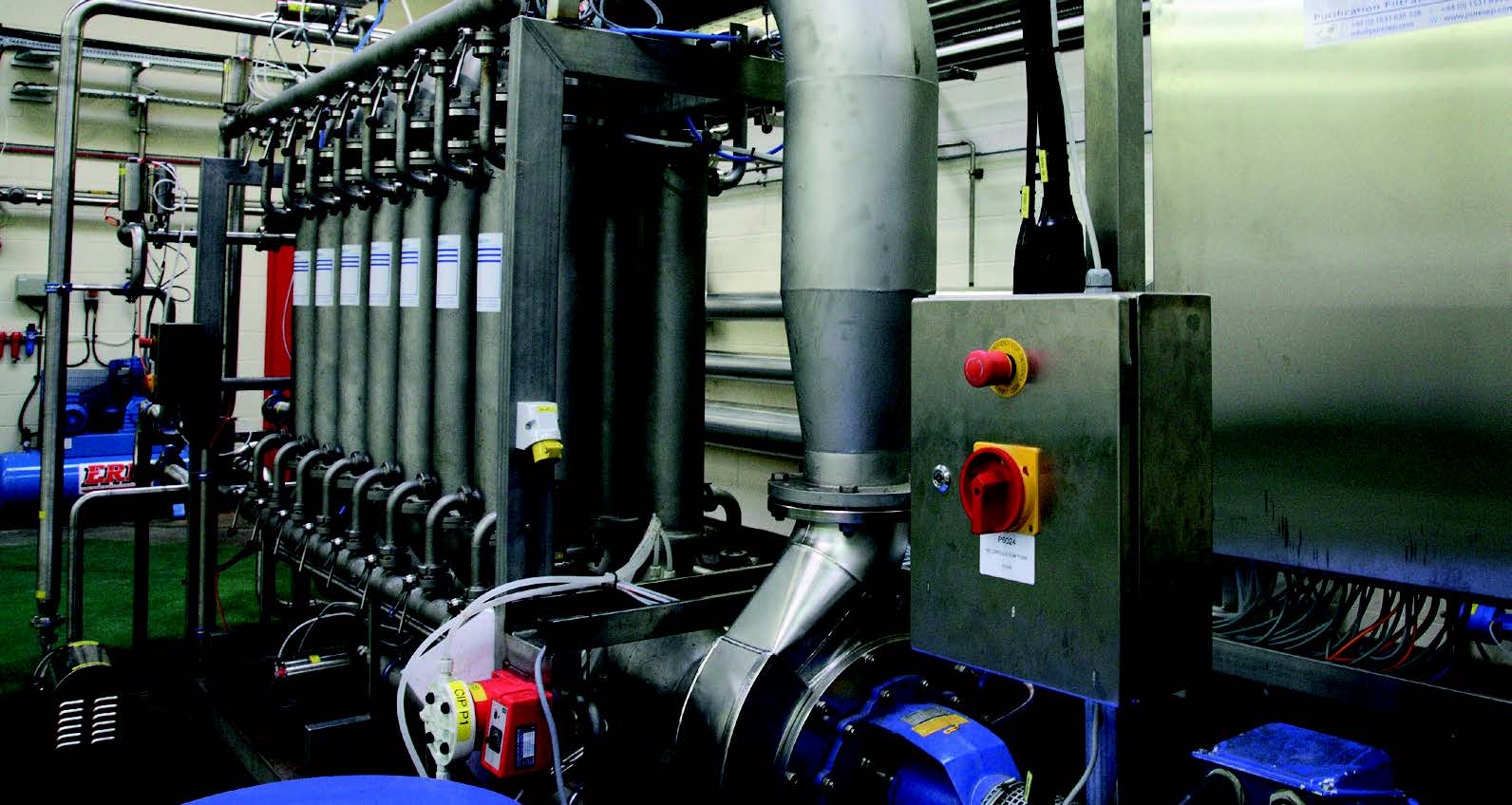
A compact design that delivers consistent quality at a low cost
Denyer goes on to say: “Filtration is an important part of any fermented beverage production. In this process yeast needed to be removed from the final product to give a consistent taste and clarity. Space was tight in this project and we needed to connect the new system quickly and efficiently so as not to disrupt a live production process. We used 3D modelling technology to plan the flows and demonstrate the final design to the Heineken team. We used the exact dimensions of the factory to plot the layout so we knew there would be no issues when we brought the kit to site. The compact design of the PureFlow system ensures that you have reliable and consistent operation all within a small footprint.”
“We are fortunate to have large manufacturing facilities, so we carried out most of the user acceptance testing here on site, it made installation and commissioning a straightforward process. The installation of the kit was carried out smoothly and with no downtime required; the operators were soon trained on the HMI and PLC and the system was live.”
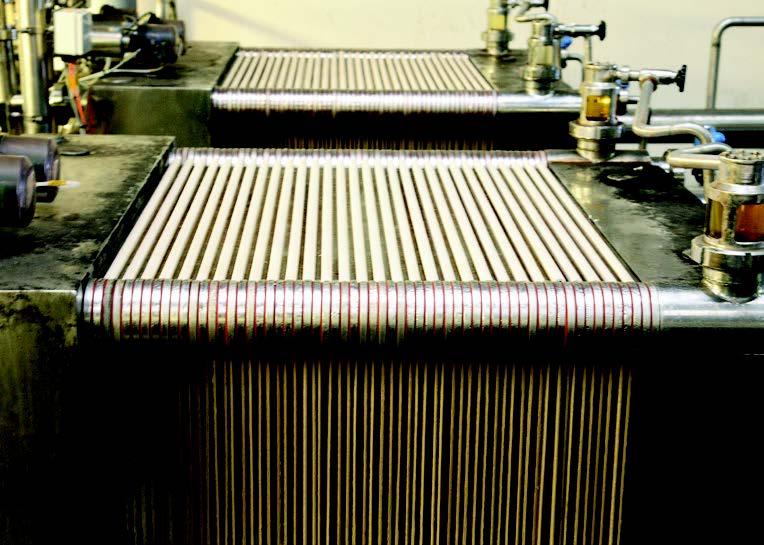
The new solution included:
- PureFlow crossflow microfiltration system – specifically developed for use in the beverage manufacturing environment and containing 2 banks of 16 membrane modules
- PLC control panel running modules for: cider filtration, flush cycles, cleaning, controlling pumps, monitoring pressure, adjust tank levels and monitoring and recording data.
“The process control software created by Envirogen Group has proved to be excellent at protecting the membranes from damage, through control of filtrate flow in a clean membrane followed by transmembrance pressure (TMP) control as the membranes get fouled and the viscosity of the retentate increases. Ramping of temperature in the ‘clean in place’ (CIP) cycles has further extended membrane life”.
Day Manager of Cider Production at Heineken.
Key outcomes
- Production output increased with no need to run back-pulsing programmes
- Increase in yield from the plant, due to diafiltration methods
- Cost per manufacturing unit decreased, due to operational efficiency improvements
- Peace of mind for ongoing performance with ongoing service and maintenance plan
For a free assessment to evaluate water treatment and process filtration solutions for your site, contact our team of expert engineers
About the client
Heineken are the UK’s leading cider and beer producer employing 2,000 people across the UK. Established in 1864, they manufacture many popular brands such as Bulmers, Strongbow, Kronenburg and Fosters.
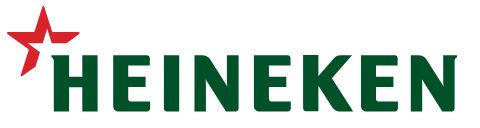