Frustrated with the high cost of mains water, a leading UK-based convenience food manufacturer started to investigate the possibility of reinstating two boreholes at its Selby site in North Yorkshire. With high levels of arsenic and iron present in the borehole water, the manufacturer was concerned that it couldn’t be treated to a high enough standard at a reasonable cost. Following a tender process, Envirogen won the contract to install a complete borehole water treatment system to treat the borehole water to meet the UK’s Drinking Water Inspectorate (DWI) Private Water Supplies Regulations. The plant efficiency and the resulting savings are so great that the plant will generate payback in just three years.
Borehole water solves an expensive problem
This food manufacturer supplies convenience products to large brands across the UK. Several products are made on-site, including pasta and curry sauces and pickled vegetables that depend on water as an ingredient. As a result, all process water streams must meet drinking water standards. Incoming streams are also used as boiler feedwater, after passing through an existing softener and reverse osmosis process.
Mains drinking water has long been used as the source of all water on the site and although two existing boreholes had been used in the past to provide cooling water, the levels of arsenic and iron in the water made it unsuitable for process use. However, with water becoming a larger cost as the business grew, the management team were looking for alternative sources. The solution would need to provide a consistent and safe supply of purified water to drinking water standards while helping the site to meet its environmental and water reduction targets. The team was also concerned about whether a borehole water treatment plant could provide the efficiencies needed to create fast payback and reduce on-site operating costs.
“Boreholes are an excellent way to cut water costs,” explains Chris Allen, Project Manager, Envirogen. “Although Yorkshire Water limits the extraction rates for borehole water, the amount that can be fed into the system dramatically reduces the mains water rates.”
“Our client was concerned about the levels of trace metals, such as arsenic, iron and manganese in the borehole water. Arsenic levels were more than double the required drinking water standard limit at 25 parts per billion (ppb) and iron levels were well above the limit at 5 parts per million (ppm). However, the most advanced borehole water treatment systems are more than capable of meeting drinking water standards and they do so at a fraction of the cost of buying in pre-treated mains water.”
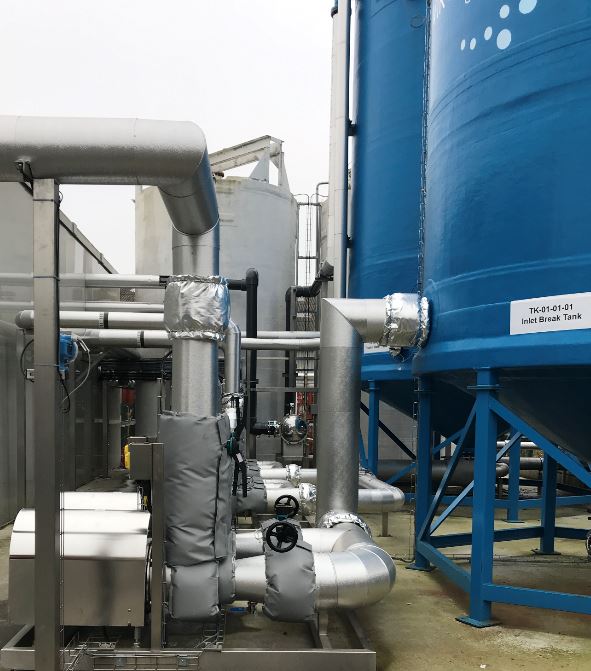
Chlorine dosing in the inlet break tank oxidises trace metals
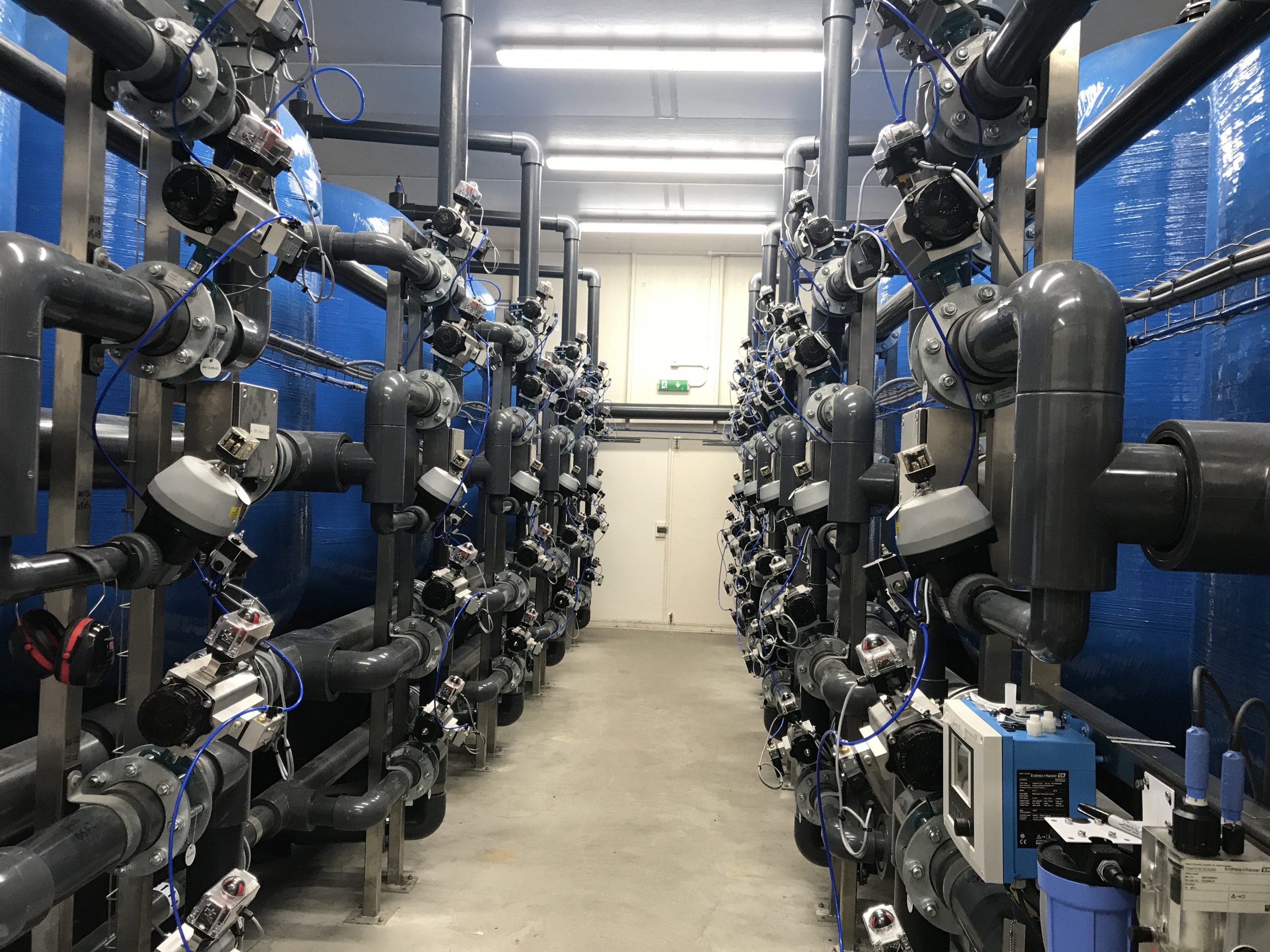
Multimedia filters remove suspended iron, arsenic and manganese
A modular system design saves valuable factory space
The manufacturing site had limited space but a strip of land along the side of the building was available for a self-contained solution. Envirogen worked with a third-party contractor to design and construct an outbuilding for the borehole water treatment plant and then built the system from pre-designed modules to slot in through the roof space.
The borehole water treatment plant:
- Takes borehole water to an inlet break tank where the water is pre-dosed with sodium hypochlorite and ferric chloride to oxidise iron, manganese and arsenic and convert them from soluble to insoluble salts.
- High-pressure pumps then send the treated solution through multimedia filters, comprised of catalytic media, sand and gravel. This media acts as a physical filter to stop suspended metals from passing through.
- The water then passes through activated carbon filters that scrub the water to remove the chlorine, odour and taste, passing it to a treated water tank.
- Before the water is sent into the factory, it is dosed with a residual level of chlorine to prevent any bacterial growth.
- High-pressure pumps send the water into the factory’s process streams and to the existing softening and reverse osmosis system for use in the boilers.
Chris Allen, Project Manager at Envirogen Group, said:
“The resulting treated borehole water now exceeds drinking water standards. Our tests show that the water contains no arsenic and that the iron levels are well within the required limits. The system is now up and running and delivering a very cost-effective stream of high-quality water into the factory for use directly in the manufacturer’s products. We helped the client understand the extraction limits that they will need to meet with the system but even with these limits, the borehole water treatment system will pay for itself within three years.”
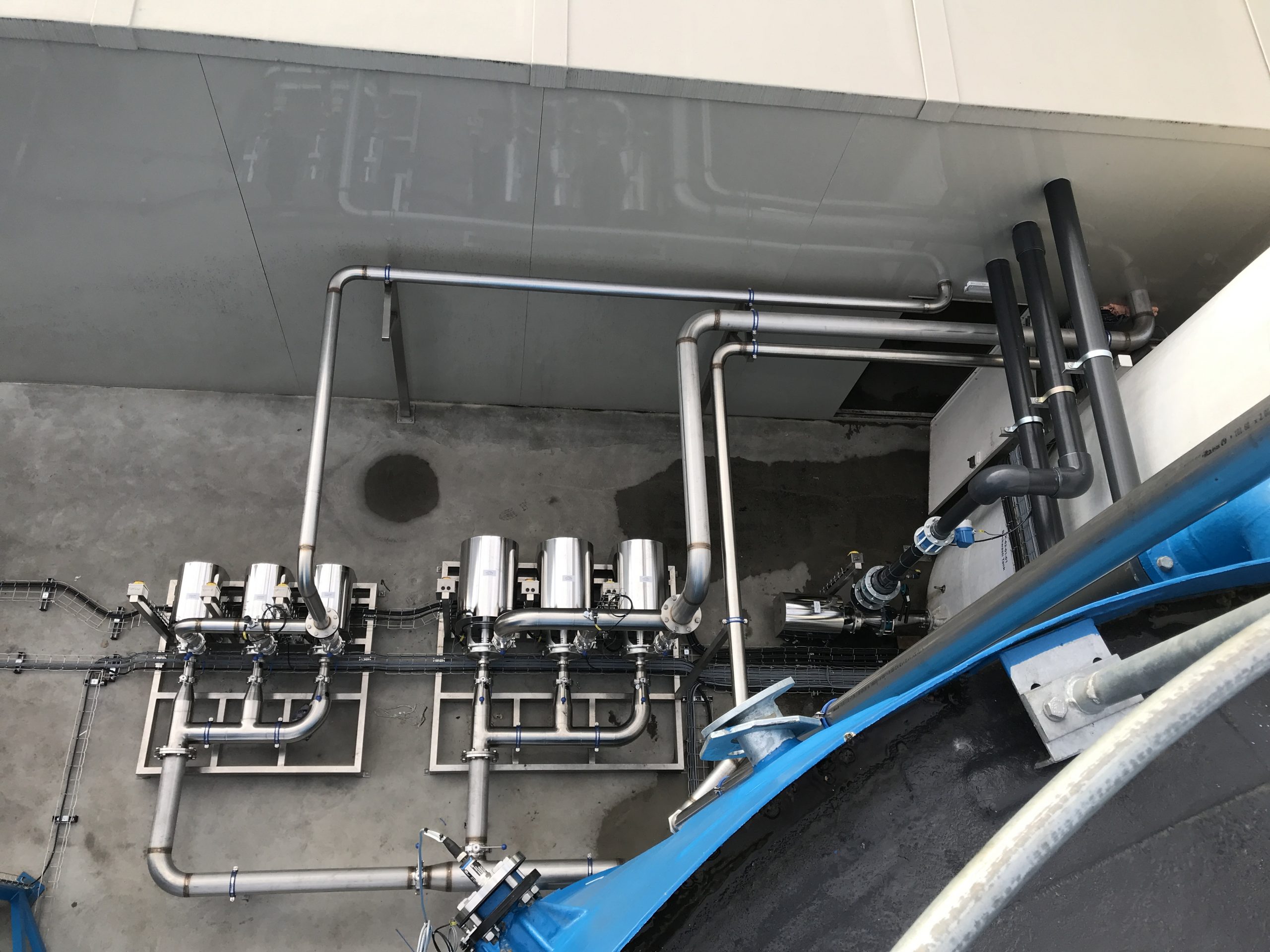
Aerial photograph taken during construction of borehole water treatment plant, Selby
Complete control for ongoing performance
To ensure that water standards are maintained, Envirogen installed a full PLC control system with a human-machine interface (HMI). Water standards are constantly checked both on-site and through digital remote monitoring by the Envirogen support team and trending historical data is recorded by the system to help evaluate efficiency and effectiveness.
For complete peace of mind, the client also took out a long-term PureCare service and maintenance plan with Envirogen. Engineers are on-site every month for continued operator training and system fine-tuning. The contract then rolls into an ongoing preventative maintenance plan with remote monitoring.
Following the success of the Selby project, the client commissioned the Envirogen team to begin work on another borehole water treatment system at its Warrington factory.
Read more: borehole water supply protected by new water treatment system, keeping production running for leading food manufacturer, Warrington
Key outcomes
- With strong project management and successful collaboration with third party contractors, the borehole water treatment plant was installed in just four weeks
- The self-contained system was built on wasteland next to the factory without impacting on day-to-day operations
- Final process water has no arsenic and iron levels at less than 100 ppb – exceeding drinking water standards
- The client is now able to extract 120 m³ of borehole water per hour for use within process and boiler feedwater
- The system will achieve payback in just three years
- The client now makes substantial savings on mains water bills
- With an ongoing PureCare service and maintenance contract, the client can be assured of consistent and reliable performance for years to come.
For a free assessment to evaluate water treatment and process filtration solutions for your site, contact our team of expert engineers
About the client
From its Selby site in North Yorkshire, UK, this food manufacturer produces ready meals and sauces for some of the largest supermarket brands.