In 2019, Vrumona, one of the largest soft drinks manufacturers in The Netherlands, came to The Envirogen Group with a complex problem. Part of its activated carbon water treatment system was coming to the end of its natural life and needed replacing, but with three million hectolitres of beverages leaving the site every year, the flow of purified water in the product line could not be interrupted.
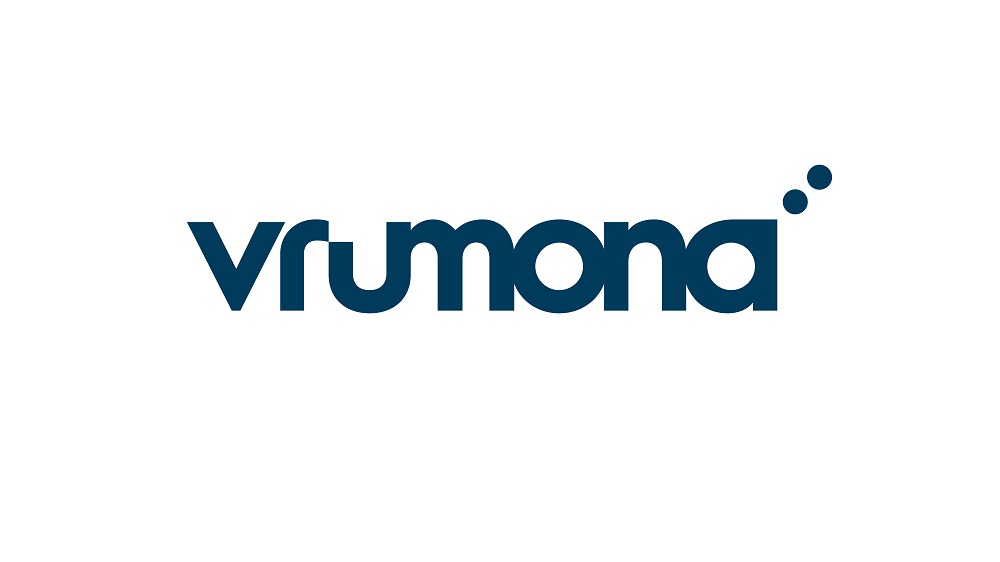
New activated carbon water treatment system feeds growing manufacturing requirements
As part of the site’s expansion plans, the activated carbon treatment plant needed to be relocated to a new building and the whole system future-proofed to grow with the business. After a successful bid, Envirogen started working with Vrumona, battling a global pandemic to deliver a new, state-of-the-art system using remote planning and robust project management, to deliver the system on time and to budget.
Being part of the Royal Unibrew group, and as a major producer for brands such as Pepsi, Sisi, 7UP and Sourcy, Vrumona must work within stringent recipes to ensure that, wherever a soft drink is manufactured, the taste profile is identical. Reaching very high standards of water purity is one element of this.
As part of a complex water purification process, activated carbon treatment was being used to remove organic compounds and safeguard against potential taste or odour taints that might affect the quality of the beverages, but the current system was coming to the end of its life. A new building was allocated for the activated carbon water treatment system that would start to feed the growing manufacturing requirements.
A robust design based on previous experience
After careful analysis of the entire water treatment process and the flow rates needed to support downstream processing and manufacturing demand, Envirogen designed a new activated carbon water treatment system. The main system consisted of three stainless steel vessels, three metres in diameter and six metres high, each containing a layer of course filtration media, overlaid on extremely high-quality granular activated carbon. The water enters the top of the vessels from the downstream ion exchange process and permeates through the media, then the activated carbon, where organic solids, taste and odour are adsorbed. The water in each tank then passes through high-flow polishing, pleated sheet cartridges in stainless steel housing.
Emil Bisseling, Sales Manager, Envirogen, explains the strategy behind the design:
“Our granular activated carbon filter systems are created to strip out impurities so that the manufacturer can start creating their beverage from a neutral position. The hygienic design complies with global manufacturing safety standards and the stringent quality and consistency metrics defined by Royal Unibrew in its recipes.
“As water treatment and process filtration experts, we were able to provide a total solution. We installed the filtration cartridges and filter housing downstream of the activated carbon water treatment so the water output is ready to use directly in the manufacturing process. This is the last treatment stage before the water becomes the product, so it must be perfect.
Service and maintenance requirements were also considered carefully in the design. The activated carbon media requires a straightforward regeneration process, controlled through the HMI (Human Machine Interface), and the long-life polishing cartridges are easily removed for exchange when they reach the end of their life. A full stock of replacement cartridges is held at the local Envirogen distribution centre for quick and consistent resupply, as and when needed.
A phased installation for continuous supply
To ensure a continuous supply of purified water, one of the vessels was replaced within the current activated carbon purification process. Once this vessel had uplifted the processing capacity of the current system, the remaining two vessels were installed in the new location. Since the flow rate of the new system exceeds the current requirements on-site, the manufacturing operation could switch to the new system with only two vessels running.
The next part of the switchover was the most critical, as Bisseling explains: “The client not only needed new hardware but also a new HMI and Programmable Logic Controller PLC) interface, with updated software, to benefit from the latest technological advances, including their preference for Lockout-Tagout (LOTO) procedures for maintenance safety. Switching a treatment plant from one set of control panels to another is the riskiest stage if it is not handled correctly.
“We worked closely with Vrumona to collaborate on the new software, and we had a joint team on-site to carry out the changeover step by step. This controlled transfer meant that the water supply simply switched from the old, activated carbon water treatment system to the new one. Our HMI is extremely intuitive, so the training requirements are low. The touchscreen guides the user through the protocols and the Vrumona technicians were running the plant the next day to achieve desired outcomes.”
Finally, the remaining new vessel was moved from the old process and connected to the new to lift the flow rate to its maximum.
Bisseling continues: “Envirogen were set the challenge of installing an activated carbon filter system without interrupting the flow of purified water in the product line. The team more than rose to the challenge, working closely with Vrumona, to build strong levels of trust and transparency. Teamwork strengthened the result, paving the way for successful delivery.”
Evelien Sanders – de Boer, Managing Director, Vrumona sums up:
“This is an important step in making Vrumona future-proof. The quality of treated water is crucial for production. Put simply, there are no soft drinks without high standards of water.”
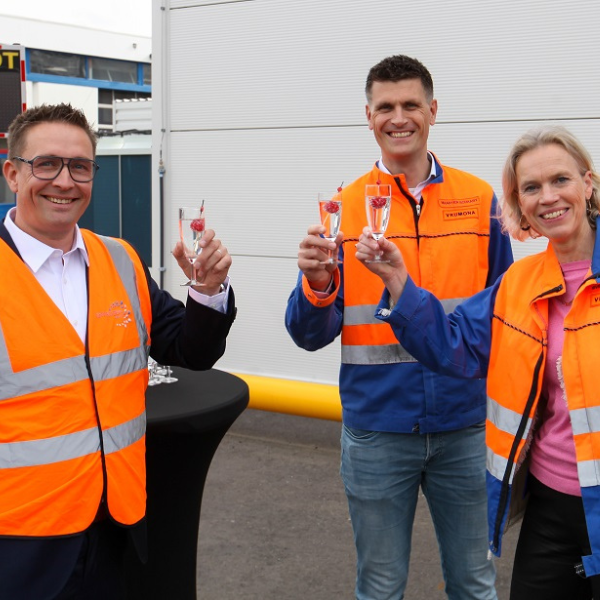
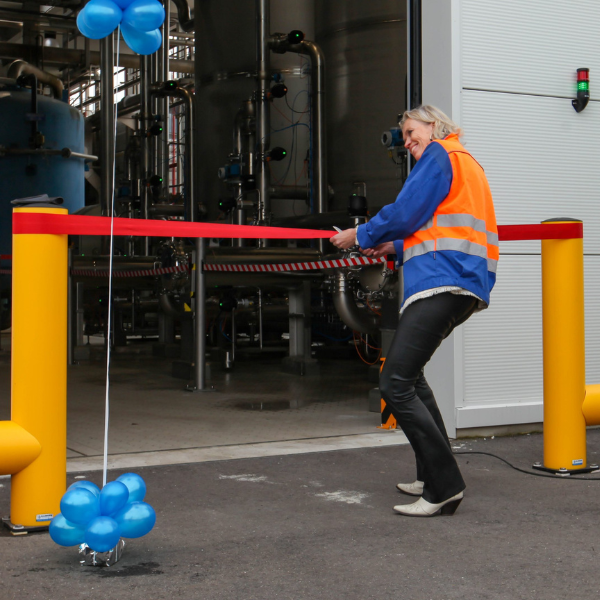
Vrumona celebrates its new state-of-the-art activated carbon water treatment system with an official ribbon cutting ceremony. Emil Bisseling, Envirogen Group, is joined by Vrumona’s Maarten Schaart, Operations Manager, and Managing Director, Evelien Sanders – de Boer.
Key outcomes
- A new activated carbon water treatment system was designed and installed, meeting flow rate requirements of 240 m3/hour but with the future-proofed capacity to reach 288 m3/hour.
- Each system meets the requirements of 9 minutes of contact time, although the system can attain 7.5 minutes if needed for future capacity needs.
- The water quality exceeds the requirements of global food and beverage manufacturing standards and those required by Royal Unibrew and key customers, such as PepsiCo.
- The system was installed within Vrumona’s stringent health and safety standards.
- High-flow, filtration housing and pleated-sheet cartridges were supplied for each activated carbon vessel as a final polishing step, maintaining high flow rates.
- Easy service and maintenance schedules are driven through the interactive and intuitive HMI.
- All replacement filter cartridges are stocked locally for easy and fast replacement.
- Multi-stakeholder engagement and unified approach with Vrumona, to deliver the system on time and on budget.
For a free assessment to evaluate water treatment and process filtration solutions for your site, contact our team of expert engineers
About the client
Vrumona is one of the largest water and soft drinks manufacturers in The Netherlands and is part of the Royal Unibrew group. As well as producing its own brands, Vrumona provides contract manufacturing for large global customers, such as PepsiCo. Vrumona has a long and successful history, operating from its site in Bunnik for over 70 years and now produces over 3 million hectolitres of soft drinks a year.