Demineralised water is essential to operations at Solenis, a leading speciality chemicals company with a large manufacturing centre in Bradford, UK. Supplying both process water and boiler feed water, for an onsite combined heat and power (CHP) plant, the existing demineralised water plant was coming to the end of its natural life and in urgent need of replacement. After cost/benefit analysis and a thorough understanding of the needs on-site, Envirogen Group was able to offer an alternative refurbishment solution that would protect the continuous pure water requirement while saving considerable capital expenditure.

A consult-led approach protects future revenue
The Bradford site is one of 39 manufacturing operations owned by the Solenis brand, producing dispersions and additives for use in paints, inks and coatings. Demineralised water is a key process component, but 70% of the ultra pure water produced on-site is destined for the large CHP plant that produces heat and electricity for the factory and drives its production processes.
This enormous chemical manufacturing plant works 24-hours-a-day, making important, supply-to-demand chemicals. Incoming water streams must be demineralised to protect the customer’s steam turbine, boilers and process equipment. The water must also meet product quality standards, with conductivity levels less than 0.1 micro siemens (µS) and silica levels less than 20 parts per billion (ppb). With the system being over 20 years old, the current demin plant was putting water quality standards at risk.
“Envirogen had been servicing the Solenis demineralised water plant for many years,” explains Bill Denyer, UK and European CEO, Envirogen. “Back in 2016, we advised the site managers that the system was reaching the end of its natural life. Following discussions with Solenis, we were asked to provide our recommendations; although replacement was an option, it required significant investment and downtime. We spent time with the management team, understood their plans and needs for the site and combined that with our knowledge of the system. We then proposed three different options, ranging from a minor refurbishment to a complete replacement.”
Replacing and refurbishing critical components while maintaining a continuous supply
Following a successful tender, Envirogen embarked on a full system refurbishment project. All pipework to and from the demineralised water plant was replaced, from the feedstock tanks to the final treated water tank, including the chemical handling pipework. Associated automated and manual valves were also replaced. The site also required a significant upgrade to the plant control equipment, including the control panel, PLC and software. The software was reverse engineered to accommodate Siemens hardware while introducing new failsafe standards that were not in the original software.
Bill Denyer, UK and European CEO, Envirogen, explains:
“Our main concern was to protect the supply of water to the CHP system. A 120m³ storage tank provided a two-hour buffer so the supply could be considered as near-continuous. Without this water, the manufacturing system would grind to a halt and that has big financial consequences. Our refurbishment plan had to involve assurances that the operation would not be impacted while the refurbishment was underway, and we took a systematic approach with ultra-pure water generation back-up built-in.”
The refurbishment of the demineralised water plant was planned in three stages:
- Phase 1 included full replacement of all polyvinyl chloride (PVC) and polyvinylidene fluoride (PVDF) pipework and automated and manual control valves for the twin and mixed resin beds in one of the duplex streams.
- Phase 2 involved this first stream being brought back online while the second part of the duplex system was refurbished in the same way as the first.
- Phase 3 then saw the full replacement of all solenoid control enclosures, as well as the main control panel, PLC and software.
- Full factory acceptance testing and input/output testing then took place before the system went live.
A temporary water treatment plant system installed to ensure continuous ultra-pure water supply
A critical part of this project involved ensuring a continuous treated water supply throughout the works. At the request of Solenis, our solution included the supply of temporary water treatment rental equipment in the form of mobile water treatment units that were located on-site for the duration of the works. A containerised reverse osmosis system, capable of providing volumes of up to 40m³ per hour, was installed followed by an ion-exchange, mixed-bed polishing container. Together the temporary systems achieved the required water quality with conductivity less than 0.1 µS and silica levels at less than 20 ppb.
The mobile water services units were connected at the start of the project, in case of unforeseen issues during phases 1 and 2. However, the temporary mobile water treatment plants were only needed during the planned phase 3 period, when the mobile units provided full system supply as the PLC control system was replaced.
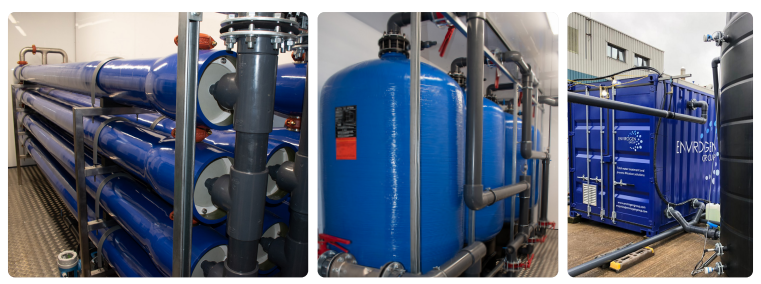
Mobile water treatment systems: A full containerised water treatment plant back-up system was provided for ultimate peace of mind throughout the project. This included a mobile reverse osmosis system, and an ion-exchange, mixed bed polishing container
Our client explains the importance of trust and reliability:
“Reliability was the most crucial factor for us. The service team at Envirogen have been looking after our system for many years and providing an excellent service. We trusted the team’s judgement and advice. They could have pushed for a new demineralised water plant, but we had open and honest discussions and they provided fair assessments and proposals based on our exact needs. We started project planning just as the Covid-19 lockdowns began so we shifted our planning meetings online. Despite this additional barrier, Envirogen created a robust installation strategy. Not once did we lose supply and the integrity of our products and the protection of our CHP system was maintained throughout.”
The installation was carried out on-time and to budget and was completed in just eight weeks. The system is now live and guaranteeing a supply of demineralised water for at least another 10 years. To ensure maximum operating efficiency, Solenis took out a PureCare service and maintenance plan. Envirogen engineers are on-site every month to check the feedwater characteristics, carry out operation and performance checks and monitor the regeneration sequences to ensure that optimum efficiency levels and low operating costs are maintained.
Key outcomes
- Entire demineralised water plant refurbishment completed in just eight weeks – including pipework, valves and new control system.
- Project completed to budget – with significant CAPEX savings versus a replacement system.
- A full mobile water treatment trailer back-up system was provided for ultimate peace of mind throughout the project.
- A sustainable stream of high-quality water is guaranteed with less than 0.1µS conductivity and less than 20 ppb silica.
- A continuous supply of purified water was supplied throughout the installation with no impact on the manufacturing process.
- A long-term PureCare service maintenance contract ensures that the plant continues to operate at maximum efficiency.
For a free assessment to evaluate water treatment and process filtration solutions for your site, contact our team of expert engineers
About the client
Solenis is a speciality chemicals manufacturer and supplier, working across 120 countries with 39 global manufacturing facilities. The Solenis Bradford site manufactures dispersants, thickeners and speciality components for use in paints, inks and coatings. These products are used in various industries such as automotive, furniture, printing and cosmetics.
