When a 15-year-old borehole water treatment plant started to fail, the rising costs associated with repairs and subsequent reliance on mains water started to increase operating costs for a leading ready-meals manufacturer. With a challenging hard-water profile, elevated levels of iron and arsenic and a precise ingredient water specification, the new system had to be reliable and robust and it was needed quickly. Having completed a successful installation at the factory’s sister plant, Envirogen Group was asked to provide a new solution to maintain the borehole water supply.
Tackling iron and arsenic to meet drinking water standards
From its Warrington site in Cheshire, UK, this food manufacturer produces ready meals and sauces for some of the largest supermarket brands. Water is a key component, both of the product and the manufacturing process, with a borehole water supply contributing to a huge decrease in costs, when compared to mains water feeds. The former borehole water treatment plant had been in place for 15 years and was coming to the end of its useful life. Although Envirogen engineers had worked on the system for several years to extend its service and maintain water standards, age-related failure was becoming a real risk. Envirogen engineers alerted the client to the issues and the wide-reaching implications that this would have for the manufacturing site. Together with the client, the team agreed that it was time to invest in a replacement water treatment system.
Envirogen recently installed a new borehole water treatment plant at the manufacturer’s sister plant in Selby, North Yorkshire. Having watched the Selby installation with interest, the Warrington team invited Envirogen to work on this new installation. Since Envirogen was already trusted to provide the service and maintenance contract for the Warrington system, the team had an in-depth understanding of the incoming borehole water supply and the treated specification.
A design to combat time and space
The feeding aquifer supplies two boreholes and has elevated levels of iron, at 50 times the permissible drinking water limit, and arsenic levels sampled at around 90 parts per billion. These had to be reduced with water treatment to meet the Water Supply (Water Quality) Regulations 2016, particularly as the borehole water supply is used directly within products. Water hardness also adds complexity. With levels of calcium and magnesium above the national average, softening is needed to remove taste taints and protect heating equipment and pipes.
“The incoming borehole water supply profile was certainly a concern for our client,” explains Chris Allen, Project Manager, Envirogen. “But we put the team’s mind at ease, having encountered more challenging incoming streams before. We knew the existing system inside and out and by combining several water treatment technologies we knew that it would be possible to achieve the water specification and deliver the system well within the client’s budget. Time was clearly an issue too, the existing system was at risk of age-related failure and we needed to make sure that a new robust system was brought online as soon as possible.
“The client identified a plot of disused land at the back of the factory that could serve as the site for the new treatment plant. The area was a challenging shape, being long and thin, and was located close to train tracks which made it difficult to place cranes to erect the building and lift in the tanks. However, we worked with an expert third-party contractor to manage the construction on the land available and we custom-designed the treatment system to fit within this area. By designing an outdoor, self-contained system, there would be no space pressure added to the busy and congested production environment.”
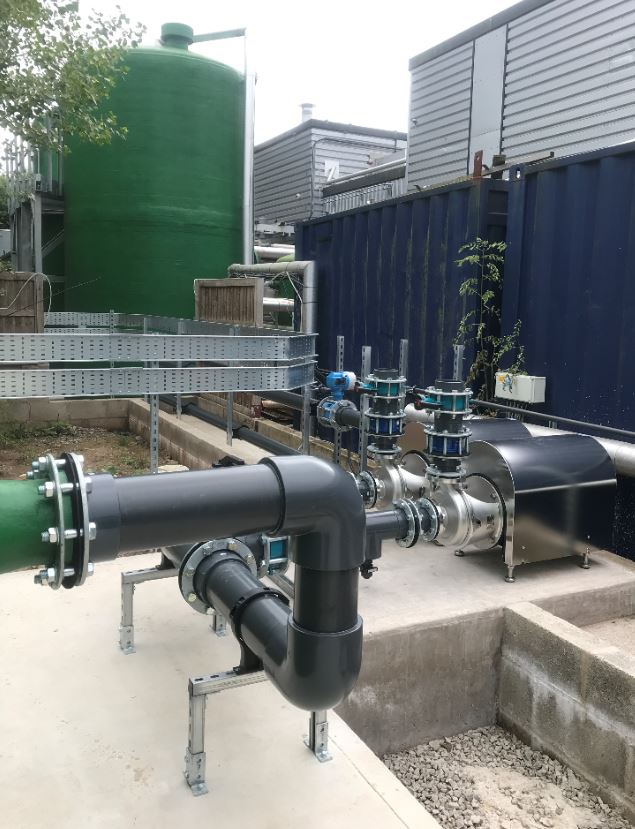
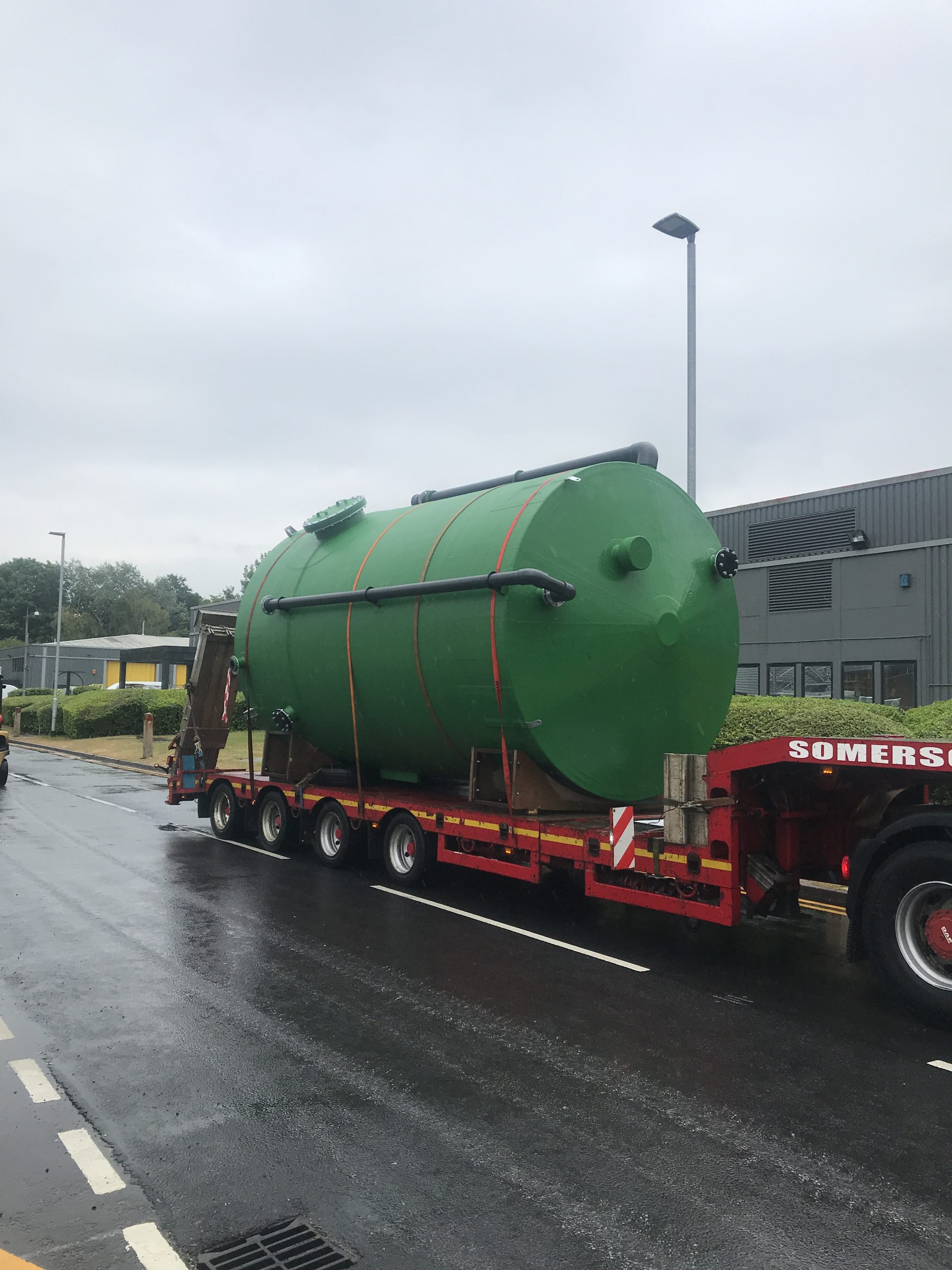
Chlorine dosing tanks and pipework installed on the strip of land at the back of the factory.
The new water treatment plant:
- Pumps the borehole water supply to an inlet break tank which is pre-dosed with sodium hypochlorite and ferric sulphate, to oxidise iron, manganese and arsenic and convert them from soluble to insoluble ions. New borehole water pumps were installed, as well as PVC pipework for one borehole where existing pipework had corroded.
- Another set of high-pressure pumps then sends the treated solution through one of four filtration beds containing catalytic media. This media captures suspended solids. With a much lower footprint than traditional media, this system helps to reduce the overall size of the plant and work within the restraints of the site area.
- The water is then passed through pressure vessels containing ion exchange resin to remove hardness, substituting calcium and magnesium ions with dissolved sodium ions.
- As a final sterilisation stage, UV filters remove any remaining microorganisms not killed by the chlorination stage.
- The treated water is tested for free available chlorine, pH, hardness and iron concentration before passing into the treated water tank.
- With a water hardness close to zero, the resulting treated water is aggressive and can cause corrosion to pipework so mains water is added to the tank to increase the hardness to 50 ppm. The water specification is achieved while protecting heating and manufacturing equipment.
- Finally, the water is fed directly into the factory’s existing water circulation system for use within the manufacturing process.
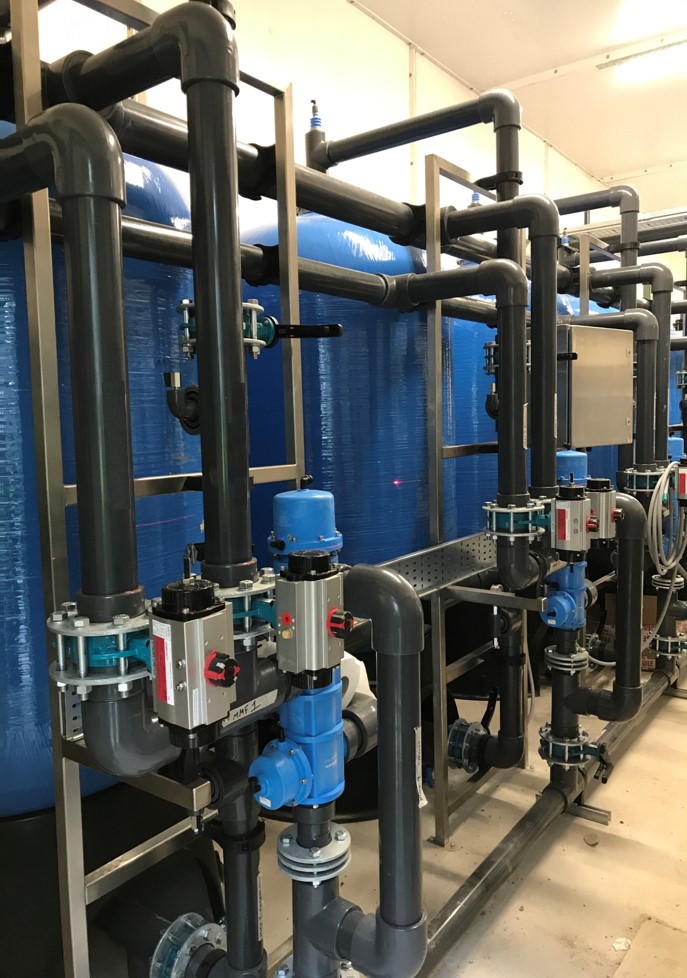
Achieving success during a lockdown
“Just as the project was due to start, the first Covid-19 lockdown was announced,” continues Allen. “Our client, quite rightly, focused on business continuity and critical manufacturing tasks for products that were now in greater demand. We applied our flexible approach to the project and replanned the installation and commissioning for when the client was happy to have us back on site. We then ensured we worked within the very strict protocols that the client and our health and safety officers enforced.
“Our client now has a robust and consistent system that treats borehole water to the required specification. With built-in redundancy, a continuous supply of treated water is ensured, even while the ion exchange and filter media regenerate. The site continues to deliver cost savings by shifting some of the reliance on mains water to more cost-effective borehole water, without compromising product standards.”
Envirogen recently installed a new borehole water treatment plant at the manufacturer’s sister plant in Selby, North Yorkshire.
Read more: borehole water supply protected by new water treatment system, keeping production running for leading food manufacturer, Selby.
Key outcomes
- A new borehole water treatment plant installed during the Covid-19 lockdown and in compliance with stringent health and safety requirements.
- A modular system was built on disused land and in a very small footprint, supplying the water requirements without compromising space within the factory.
- Unique design and catalytic media further reduced the treatment plant footprint, enabling full treatment capability within a confined space.
- Iron levels are reduced from a maximum level of 5000 µg per litre (µg/l) to less than 100 µg/l, arsenic from a maximum of 200 µg/l to less than 10 µg/l and total hardness from over 200 ppm to 50 ppm.
- The system protects the client’s bottom line, providing considerable savings on mains water bills.
- With an ongoing PureCare service and maintenance contract, the client can be assured of consistent and reliable performance for years to come.
For a free assessment to evaluate water treatment and process filtration solutions for your site, contact our team of expert engineers
About the client
From its Warrington site in Cheshire, UK, this food manufacturer produces ready meals and sauces for some of the largest supermarket brands.