Constructed within a brownfield site alongside the River Hull, Energy Works Hull is live and operational, generating enough energy to power 47,000 homes. The source of this power: 240,000 tonnes of refuse destined for landfill. At the heart of this plant is a gasification system, burning non-recyclable refuse from homes and businesses to generate renewable electricity. Protecting the plant and ensuring it stays operational 24-hours-a-day, year-round, is a stream of purified demin water.
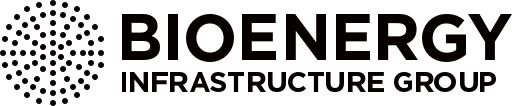
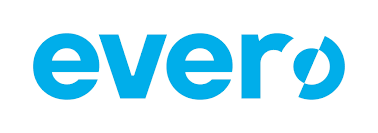
Protection through purification
“This is the latest of many waste-to-energy construction projects that we have been involved in,” explains Ian Pearson, Operations Director, Envirogen Group. “This industry is experiencing rapid growth as businesses, local councils and the Government see the benefit in tackling two of society’s biggest problems with one solution.
“Not only do waste-to-energy plants remove a large quantity of waste that would otherwise be sent to landfill but they also provide a clean and green way of producing renewable energy, without reliance on fossil fuels.”
Evero, previously known as Bioenergy Infrastructure Group (BIG), is the owner and operator of Energy Works Hull, are developing the site in ajoin venture with Spencer, Noy Fund and John Hancock through Hancock Natural Resources Group (HNRG).
Energy Works Hull is the largest of many sites managed by BIG with a generation capacity of 24MW. Although experts in gasification infrastructure, BIG required a specialised water treatment company to supply purified water streams that would ensure cost-effective, efficient, reliable and long-lasting operation of the plant.
The plant takes a feed of waste that has been pre-screened for recyclable material and burns it in a gasification chamber. The heat from this process is used to turn water into steam which is used to drive a turbine and generator to produce electricity.
Due to the high operating temperature and pressure, scale can build-up, damaging equipment and dramatically reducing the operating efficiencies of the boiler and steam turbine.
Flexible and future-proofed solutions
“Although the steam cycle is designed as a closed system, modern boilers still require a stream of demineralised water to make up for losses,” continues Pearson. “BIG needed to guarantee a reliable supply of pure water with all soluble ions and suspended particles removed. Our water purification technology is tried and tested, with modular designs that offer effective solutions with lower capital outlays and low operating costs. The industrial water demineralisation system installed for BIG delivers demin water at a rate of 5 m³/hr.”
Envirogen Group’s three-step, multi-technology, RO-EDI plant treatment uses reverse osmosis (RO) technology followed by gas transfer membranes (GTM) and finally electrodeionization (EDI) to remove all scale-forming ions that might impact the efficiency of the generator. The resulting demin water has a conductivity of less than 0.1 micro siemens (µS), with less than 10 parts per billion (ppb) silica and less than 3 ppb sodium.
Envirogen’s automated, integrated skid-mounted Eco MultiPro treatment system is modular in design, scalable and relocatable. The RO-EDI water system is future-proofed, allowing additional units to be added or upgraded to match the needs of the site and to scale-up operations, should the site capacity increase in the future. By taking the modular approach, Energy Works Hull has a flexible solution that continues to reach the greatest cost efficiencies.
“Plans for the site include supplying district heat as part of a combined heat and power (CHP) solution,” says Pearson. “This system will allow expansion so that additional utility demin water can be created should the on-site demands change.”
“We have incorporated the very latest industrial water demineralisation technology with our RO-EDI, next-generation, skid-mounted demin water system. Traditional systems would include resin beds, which process water in batches and require chemical regeneration in between. This means storing and handling chemicals on-site and incorporating additional health and safety procedures. In addition, this chemical regeneration creates an effluent stream that needs to be processed and pH balanced. Our RO-EDI skid requires no chemical regeneration, relying instead on a small amount of electricity to renew the membranes. As electricity is generated on-site and the whole process carries a much lower operating cost versus a resin-bed solution, the RO-EDI water system was the ideal solution.”
“This is just one way that we ensure low running costs,” continues Pearson. “Capital outlay is often the key consideration for procurement teams but the operating cost is equally important when gauging the payback period and the total value of water purification technology. We build a low-cost operating model into every element of our design.”
“We provide membranes, filters and consumables that last longer and need replacing less often. Our reverse osmosis membranes are durable and long-lasting which delivers considerable cost savings to our clients.”
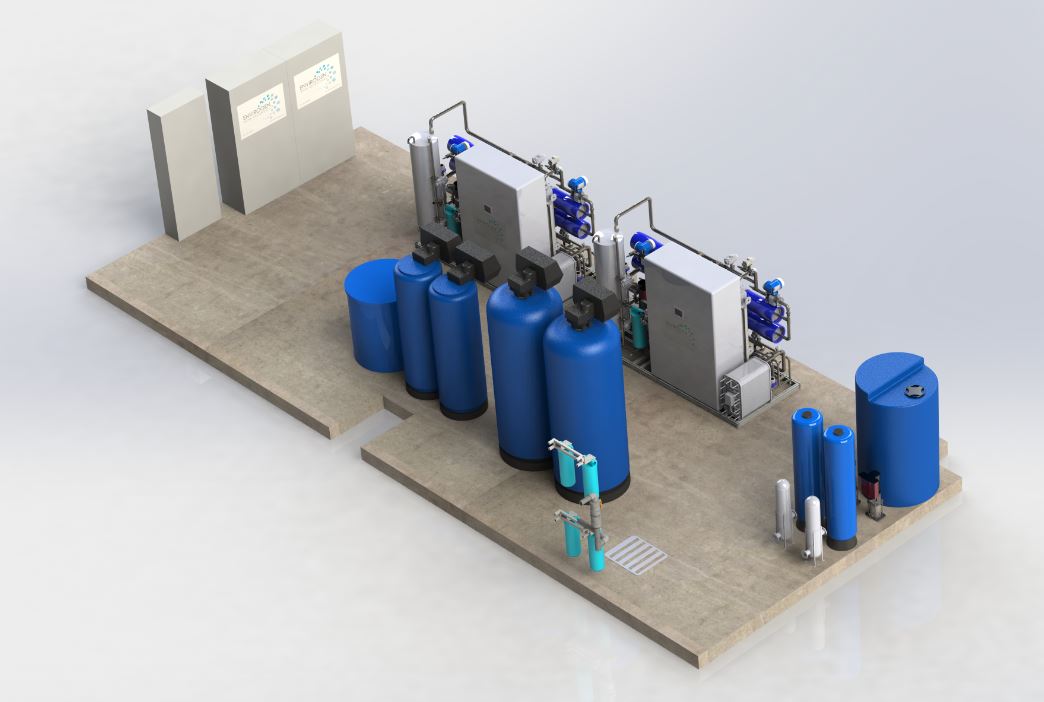
3D model designed to show the final demin water plant installed at Energy Works Hull
Taking the total solution approach
“Our clients often tell us that our value lies in our total solution approach. We don’t just design water purification technology, we install and commission it too, provide the ongoing after-sale service and maintenance to ensure long and efficient life. We also add value through the supply of specially selected process filtration consumables with a low total cost of ownership.”
This total solution approach extends throughout the client’s site too. Envirogen conducted detailed studies of the incoming town’s water and designed a bespoke pre-treatment system based on granular activated carbon (GAC) filters and softener resins to protect the upstream demineralisation plant.
“We worked with the BIG team at all stages to ensure that the industrial water demineralisation plant would be delivered and installed within the project timescales. Of course, BIG wasn’t our only project stakeholder and we worked with multiple engineers onsite to streamline individual workstreams. Collaboration was key; the project would only be a success if all individual parts came together at the right time and in the right way. Our mission is always to add value and to use our unique understanding of water treatment to help steer the project in the most time-efficient and cost-effective way.”
Energy Works Hull is now live and operational, supplying the equivalent of 47,000 homes worth of power to homes and businesses throughout Hull. 240,000 tonnes of refuse will be diverted from landfill and this, along with less reliance on traditional power generation, saves 35,000 tonnes of carbon dioxide per annum.
Interested in other power plant water treatment process projects?
For more information on other water treatment and process filtration solutions for the power and energy industry:
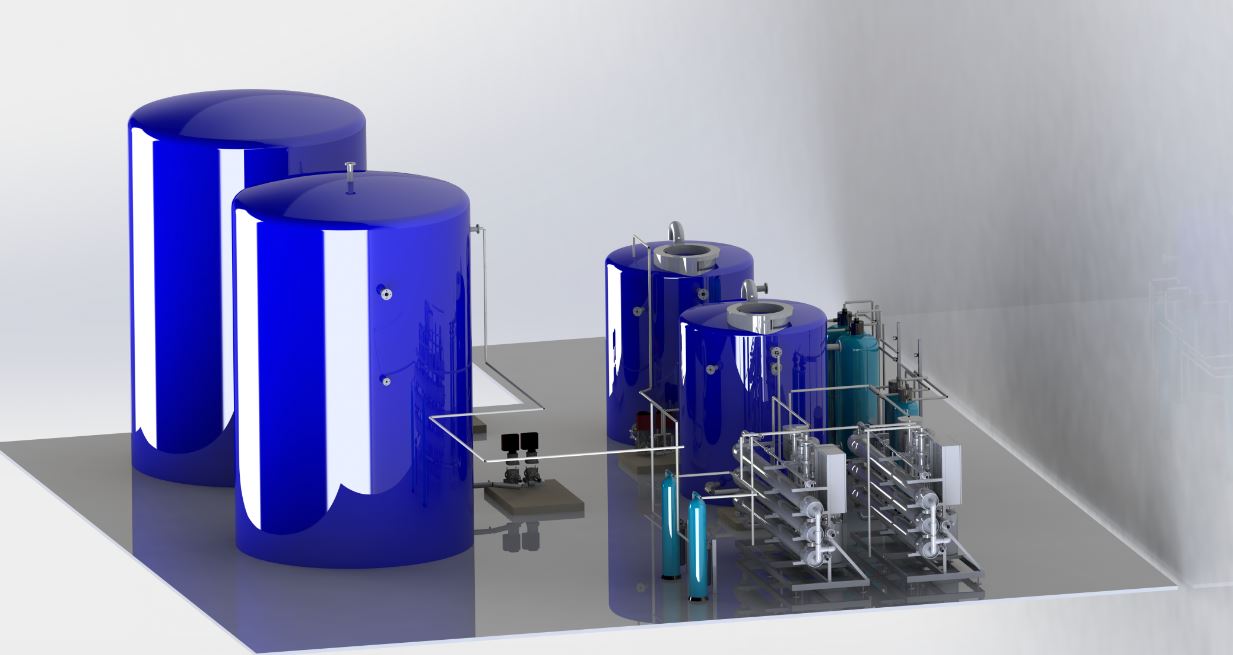
Learn how a combined reverse osmosis and electrodeionization system (RO-EDI) helps Eco Park Surrey process 40,000 tonnes of kitchen waste and 50,000 tonnes of general refuse waste a year
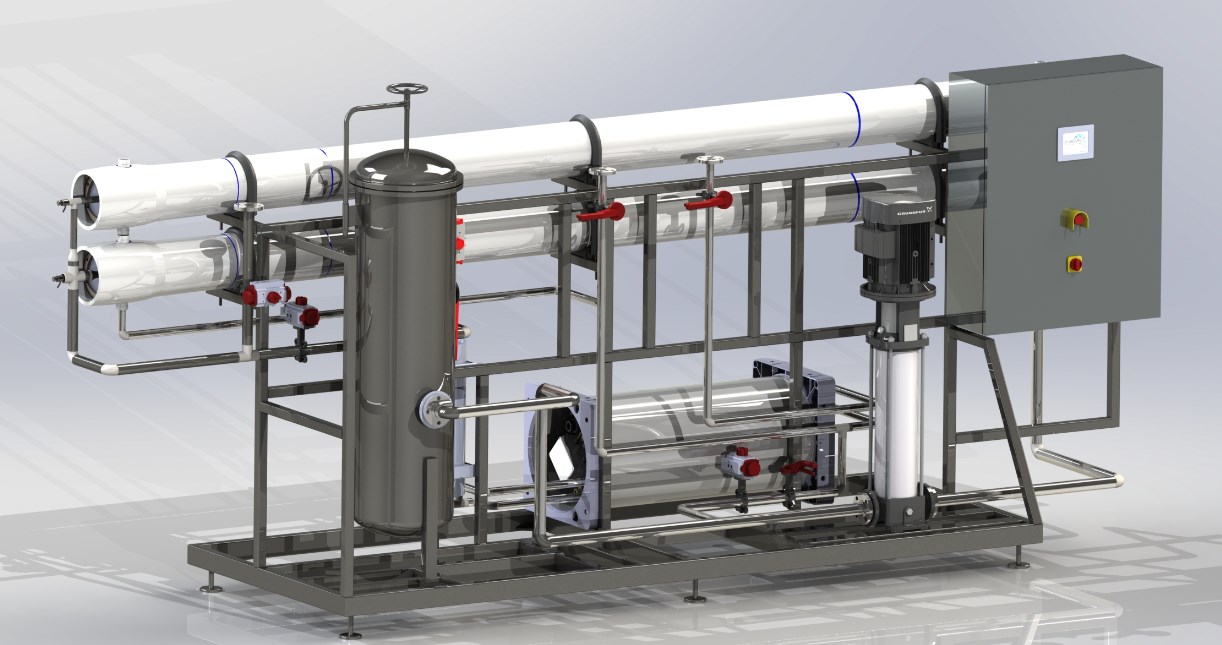
Discover how all-in-one Eco MultiPro RO-EDI water system helps energy-from-waste (EfW) plant process 169,000 units of refuse-derived fuel (RDF) each year to supply the UK’s National Grid.
Key outcomes
- A complete skid-based industrial water demineralisation system installed to produce demin water at a rate of 5 m³/hr
- Modular, future-proofed design for flexibility and scalability
- Process water conductivity reduced to 0.1 micro siemens (µS)
- The latest electrodeionization technology installed with no chemical treatment required
- Free electricity generated on-site is used to recharge membranes
- A solution that meets the needs of a large and diverse group of stakeholders
For a free assessment to evaluate water treatment and process filtration solutions for your site, contact our team of expert engineers
About the client
Evero is a renewable energy provider and investor specialising in biomass and waste-to-energy plants, with a leading position in the UK’s biomass and waste-to-energy sectors. Evero is dedicated to transforming the way society thinks about waste, following the growing demand for carbon-neutral energy sources from the increasing electrification of the UK economy. Evero’s UK-based plants have a total capacity of 145MW, and divert around 1 million tonnes of waste from landfill every year to use and generate energy.
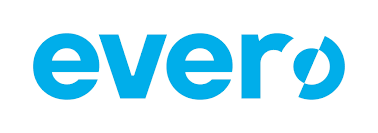