Maintaining a reliable and sustainable utilities supply is one of the key challenges for the manufacturing sector. Ensuring water volumes are continuously achieving the highest specifications whilst simultaneously maintaining suitable volumes is key. A bespoke ion exchange water treatment system comprising of counter current, packed bed, ion exchange skids and mix-bed polishing has allowed our client to achieve these aims.
The manufacturer is a world leading, multi-national producer of paper and packaging that specialise in the production of virgin fibre cartonboard. When faced with the dual issue of tightening water specification due to a high-pressure boiler upgrade, and an existing water treatment system reaching the end of its service life, they wanted to explore the best technology options to meet their changing circumstances.
Upgrades to a boiler capable of operating at a pressure greater than 40 bar meant feedwater qualities having to meet the criteria laid out in EN 12952-12. A continuous water supply with low conductivity of <0.2microsiemens/cm and silica content <20ppb was critical.
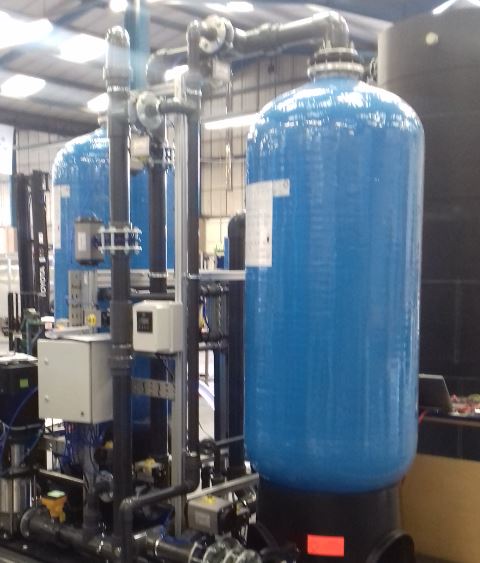
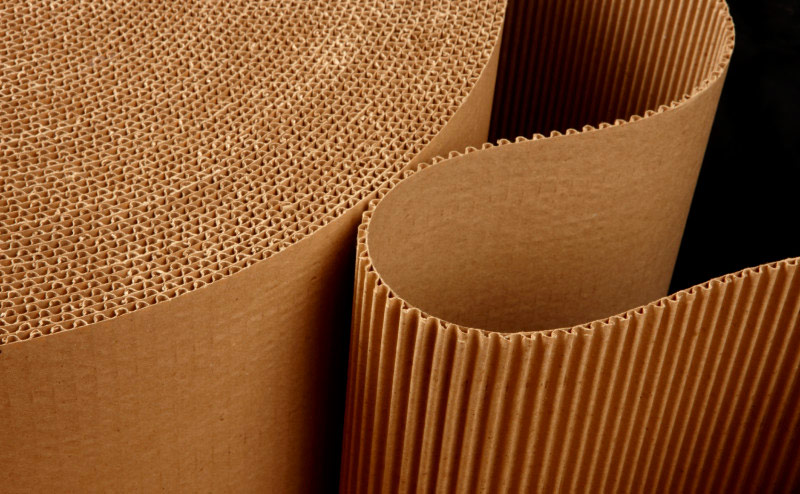
Working together and maintaining production
“The Envirogen Group has worked with process critical manufacturers for many years”
Bill Denyer, UK and European CEO, Envirogen Group.
As a major business in the packaging industry, it was key that our client maintained power and steam to site to maintain production. During the initial consultation, we worked closely with the customer and felt the application was ideal for an ion exchange water treatment system comprising a of two EcoPure ion exchange skids.
These units offer high purity water thanks to packed bed, counter current, ion exchange columns. Market leading control software means the water output is delivered at low operating costs.
We worked closely with the client to develop an innovative installation solution which places two EcoPure ion exchange skids at the heart of their treatment critical process.
See how we did it here:
In-house experts were used throughout the design, installation, commissioning phases
Our engineering team developed an innovative implementation plan which removed the need for temporary mobile water treatment units:
- Installed new EcoPure skid 1 system in a temporary location
- Decommissioned and removed old system 2 and installed new EcoPure skid 2 so that it runs in unison with new EcoPure skid 1 and old system 1
- Decommissioned old system 1 whilst new EcoPure skids 1 and 2 continued to run
- Moved new EcoPure skid 1 system from temporary location over to its permanent position
- Achieved optimal operation of new Ion exchange water treatment system via total upgrade and successful implementation.
The solution – Ion exchange water treatment system
- To deliver water continuously the plant design consisted of two EcoPure skids linked to a central PLC control system. Siemens PLC equipment and inverter drives help to deliver robust, economic performance through every process stage of the units’ design.
- Envirogen provided a full system package inclusive of bulk chemical storage solutions.
- UK manufacturing of the skids allowed for a functional FAT prior to delivery. With project management and process engineering service being provided from the UK to support the Envirogen team based in the Netherlands.
- Envirogen’s expert process engineers used throughout the design, installation and commissioning phases of the project.
For a free assessment to evaluate water treatment and process filtration solutions for your site, contact our team of expert engineers
About the client
The manufacturer is a world leading, multi-national producer of paper and packaging.