Advanced 3D modelling techniques and engineering innovation led Britvic to significantly reduce their wastewater discharge at their Beckton site – far exceeding their original targets. This modified water recovery plant system, built around existing technology and fully integrated with their current production line, led to huge additional cost savings.
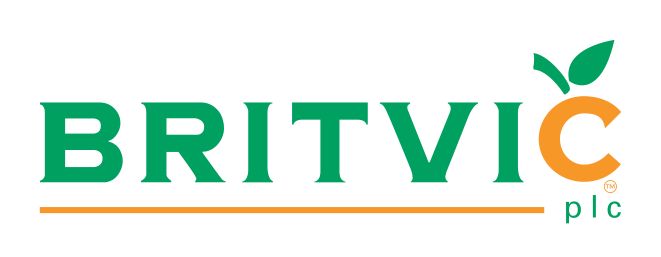
Bill Denyer, European CEO at Envirogen Group, was involved in the original meetings to assess the problems faced.
“An audit had taken place of the wastewater streams at the plant and Britvic were keen to make changes to achieve their ambitious environmental goals, as well as meet their targets to improve efficiencies and drive further cost savings on site. The changes had to happen fast, and, as always, with no impact on the day to day production output.”
“This is a very successful operation with a high output and, like many of our clients, there is very little room for downtime on production lines; the factories are working at high capacity and demand for product is only just met by production capabilities. However, it was important, for environmental compliance, that Britvic reduce their wastewater output.”
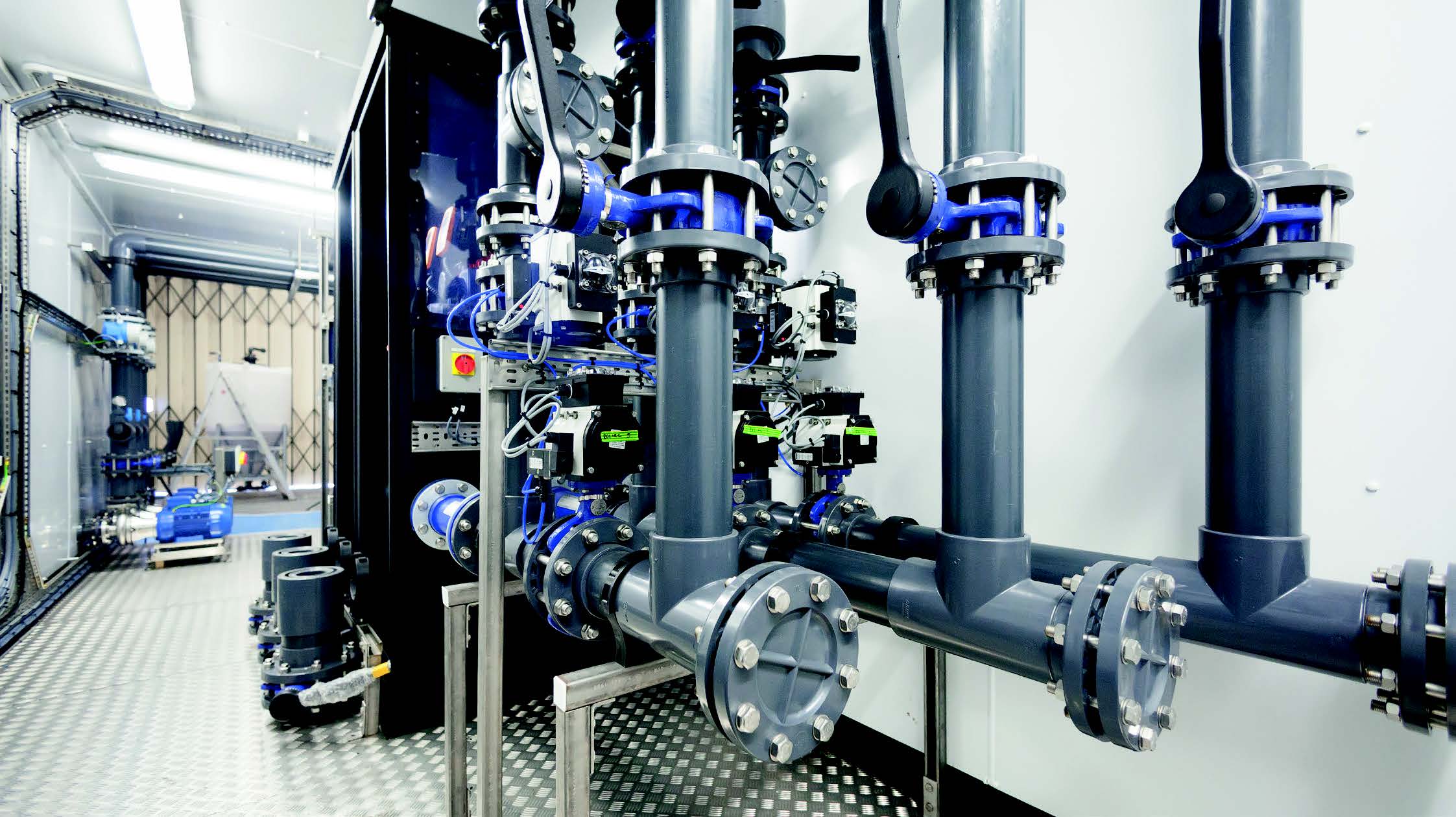
Detailed water recovery plant 3D modelling unlocked environmental potential
Denyer goes on to say: “The potential for saving and reusing water lay in the four bottle rinsing line as high quality rinse water was being sent straight to drain as wastewater. This water had been through dealkanisation processes and was UV sterilised and filtered. There was enormous reuse potential here, but we needed to ensure that the water quality wasn’t compromised. Monitoring and further process treatment would be essential to maintain sterility.”
“We drew up detailed 3D models for a sterile recapture and storage system so that this water could be fed back through to the rinse lines. The models enabled the team to see how the new kit would fit with the existing machinery and, since space was tight, we used laser measuring to ensure that the exact proportions of the factory were incorporated into the design software.”
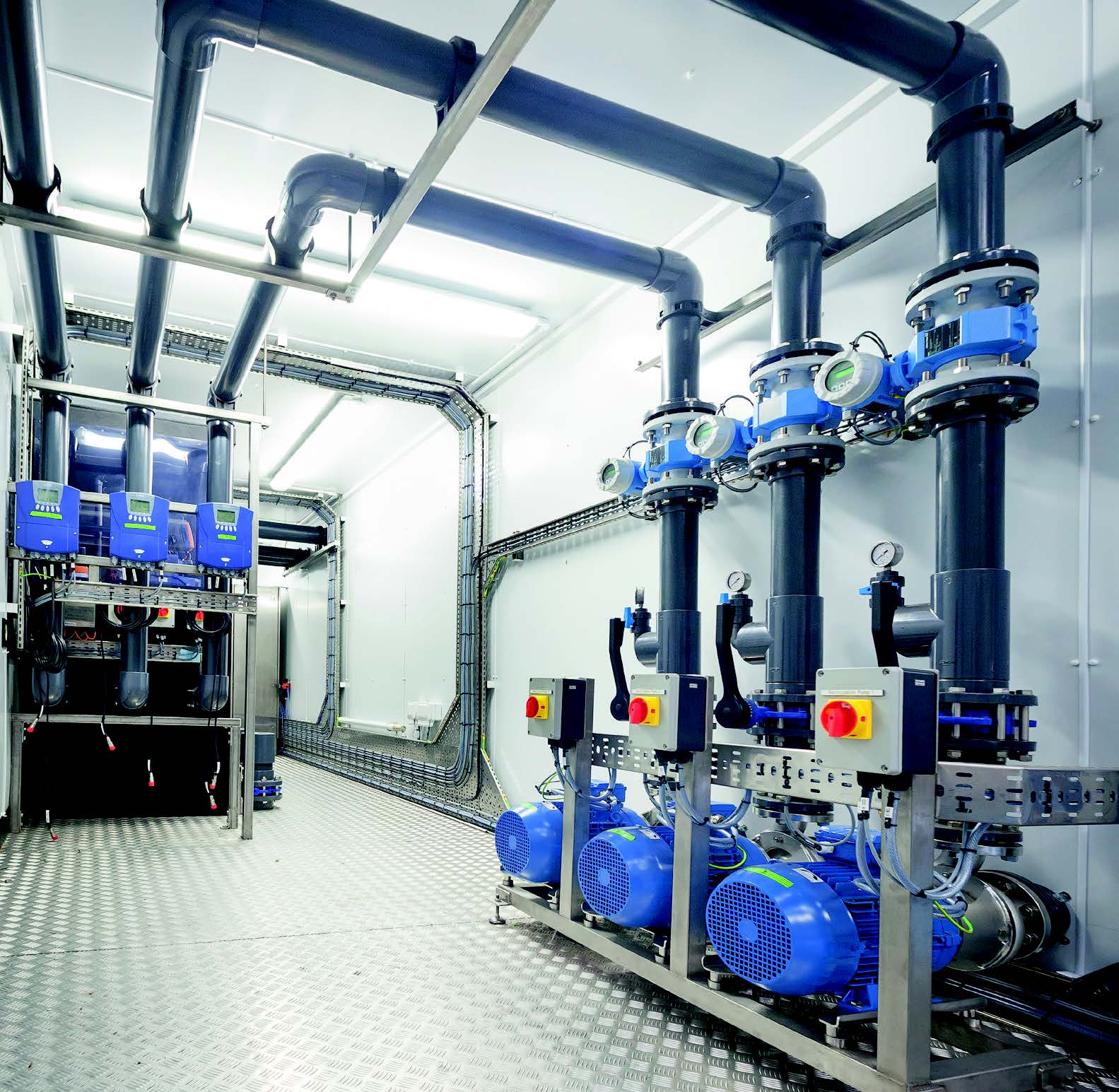
The new solution included:
- A wastewater recovery recapture line and pump system fitted to rinsing lines leading to a single storage tank
- Inline instrumentation to monitor the water quality as it is fed through to the tank, all controlled with an HMI & PLC
- In-tank monitoring equipment with pre-set quality parameters controlling discharge and refill protocols, if quality standards reduce
- Additional UV sterilisation and 10μm and 1μm absolute cartridge filtration system using long life Envirogen brand cartridges
“…Envirogen Group’s expertise and knowledge enabled them to see how modifications to an existing system could bring major benefits. Envirogen project managed the whole process from design and installation to commissioning. Their attention to detail and onsite work is outstanding.”
Calvin Winch, Operations Development GB & Ireland at Britvic
Read more about Britvic water treatment and process filtration solutions:
Key outcomes
- Significant wastewater reduction – exceeding clients targets
- Additional huge cost savings
- No operation downtime, with plant integrated seamlessly with existing equipment
For a free assessment to evaluate water treatment and process filtration solutions for your site, contact our team of expert engineers
About the client
Britvic is a leading soft drinks company, with operations in Great Britain (GB), Ireland, France and Brazil. Britvic manufactures a range of its own brands, including Robinsons, Tango, J2O and Drench as well as PepsiCo’s soft drinks, including Pepsi and 7UP. Britvic is the largest supplier of branded soft drinks and the second largest supplier of carbonated soft drinks in GB. The Britvic Rugby factory produces half of the group’s total manufacturing output.
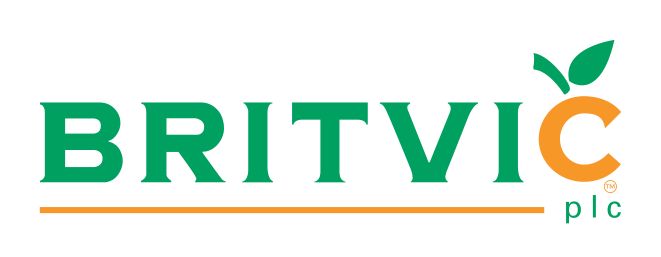