Author: Joe Higgins, Group CEO, Envirogen Group.
Water is at the front line of environmental crises and has been for over a decade. Driven by climate change, growing populations, increasing economic activity and poor water governance in both public and private sectors, water scarcities are causing regional emergencies around the globe, with implications for industrial companies across all sectors. Joe Higgins explores how companies like Envirogen can help businesses develop effective solutions.
Global shortfalls in the water supply are predicted if current consumption and production patterns do not change. According to a study by the Organization for Economic and Cooperative Development (OECD), worldwide water demand is expected to increase by 55%*, with demand for water in manufacturing expected to increase four-fold by 2050.
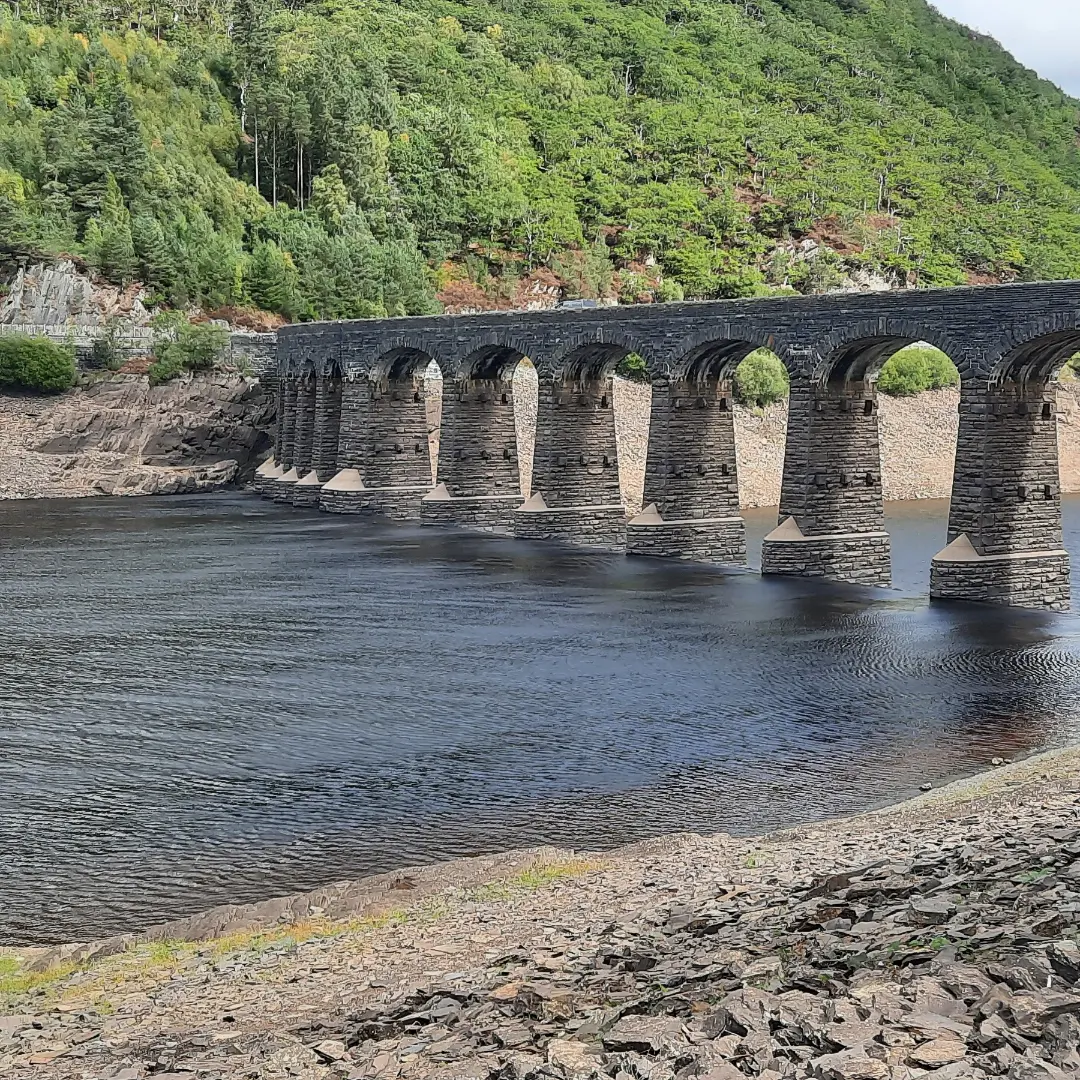
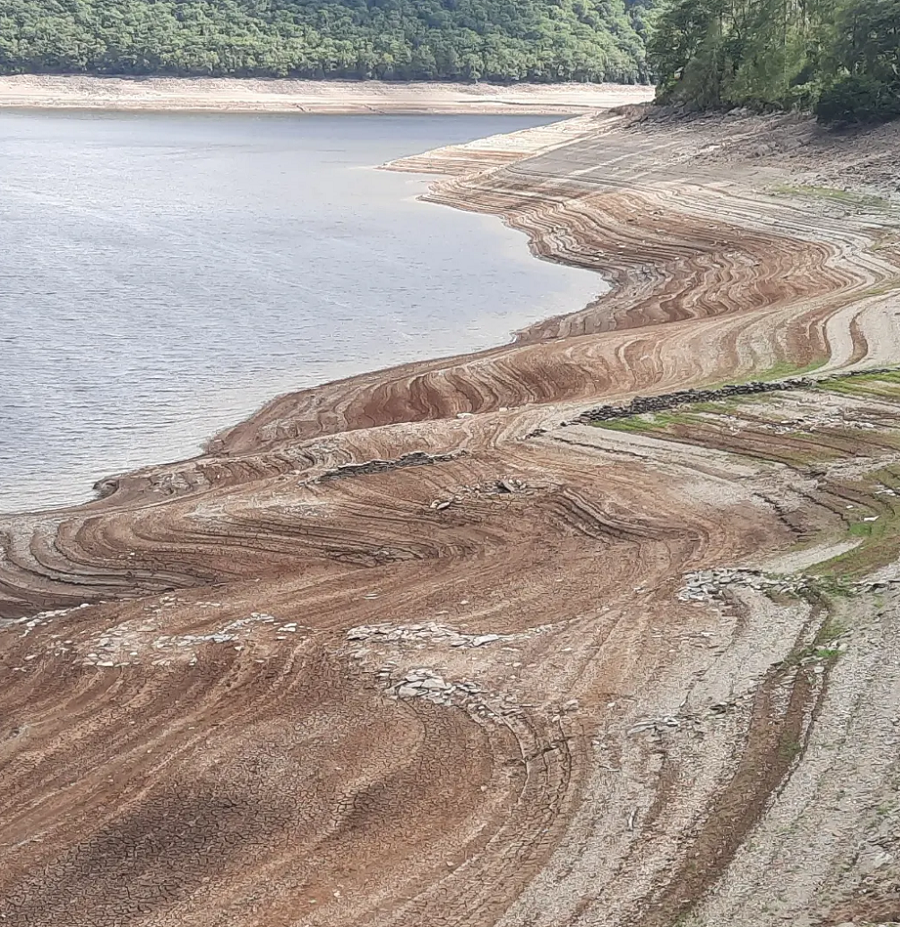
The Elan Valley (Mid-Wales) reservoir has its banks on show following Summer 2022 droughts.
Its primary purpose is to supply Birmingham, UK, with water, as well as Herefordshire via the river Wye.
Building water-resilient business models
Most industrial processes utilise water as a component of the final product, part of the production process, or even indirectly, through energy use. Substantial volumes of water are consumed by industry.
Companies in sectors such as food and beverage, energy, chemicals, pharmaceuticals, and mining account for 70%** of the world’s water use. They have the opportunity and may be required by legislation, to play a critical role in the transformation to a water-secure world by conserving water and maintaining low energy and waste operations.
Building water-resilient business models is one of the most pressing challenges for those interested in developing a safer, more circular, and sustainable industrial economy. Finding commercially efficient ways to lessen the impact of water withdrawals via water recovery, recycle and reuse becomes more critical than ever. It can happen and is happening.
Percent Increase of Water Demand
Visual representation of OECD Environmental Outlook to 2050 (from 2000 baseline):
Saving water simply makes good financial, environmental, and social sense
Water security and resilience is emerging as a core strategic consideration among many manufacturers. In the wake of extreme droughts, some of them very long-running, and exposure to water stress, more and more manufacturing companies are recycling wastewater whenever reuse can be implemented as a feasible, cost-effective option.
Manufacturers are taking control of their water management with on-site “behind the fence” solutions, resulting in increased investment in water reuse to maximise the use of water in the plant. Operational efficiency and sustainability can be expected to increase, along with improved production capacity, due to the increase in available potable water.
Limiting dependency on outside water allows manufacturers to leverage reuse to reduce water supply costs, moving them closer to zero liquid discharge systems, with the added benefit of reduced discharge costs. Businesses can also demonstrate corporate social responsibility (CSR) commitments via water stewardship which, for consumer-facing brands, are of direct economic value to companies. We have instigated numerous re-use / recycle projects where there is a significant return on investment, generally within 2 years, thereby not only reducing water footprint and improving system resilience but also supporting operational efficiency through cost reduction.
Those companies that are perceived to have better environmental practices may see improved brand value, a subsequent expansion in sales, and, where they are listed, an improvement in share price. On this subject, the investment landscape has been broadened and deepened through the addition of environmental, social, and governance (ESG) opportunities, for example, in ESG investment trusts and funds and individual ESG stocks.
Identifying industrial wastewater reuse opportunities
Numerous methods can be considered, depending on the quality and volume of the water to be recycled, as well as reuse applications. Industries can recapture and process wastewater that would otherwise be lost to trade effluent whilst in many cases incurring discharge costs, and recycled water can be used for a variety of applications. Included among the applications are washing, rinsing, plating, spraying, coating, cooling, boiler water make-up, cooling tower make-up and fire suppression systems. In some cases, their effectiveness will be impacted by space constraints and budgetary considerations.
The degree of treatment required varies according to the specific reuse application and associated water quality requirements. Water reuse generally takes place by combining several processes or technologies – depending on the case – such as biological or physicochemical treatment, solids separation, gravity and/or membrane filtration, evaporation, disinfection, membrane or ion exchange demineralisation, and advanced oxidation. We provide value engineered solutions implementing all of these technologies.
Finding a treatment solution that’s right for a company’s specific needs begins with answers such as these to the following questions:
“What volume of water is sent to drain and what quality is it?”
Reaching a sustainable, cost-effective solution is paramount, and companies will need sufficient data to make informed decisions. Typically, this will mean measuring peak flow rates, volume, quality and cost of water sent to drain, as well as benchmarking against international high performers. A thorough analysis, including return on investment (ROI) and payback calculations, can help determine what type of water reuse system is needed in a facility and which recycling measures will pay off both from sustainability and cost perspectives – and in line with water treatment obligations.
“For what applications can we reasonably use reclaimed water and where are these located on-site?”
It’s important to look at the manufacturing system in its entirety. A complete process flow diagram of a plant serves as a great overview of the process in determining which streams can be reused and where. Water reuse applications include, but are not limited to – washing, rinsing, plating, spraying, coating, cooling, boiler water make-up, cooling tower make-up and fire suppression systems.
It is recommended to start with high-volume reuse applications that have lower water quality requirements, therefore requiring less treatment. By following this approach, the facility will achieve the greatest return on investment, as higher levels of treatment increase cost. In many instances, it’s more straightforward to capture and recycle wastewater at the source (i.e., directly after a manufacturing process and before it reaches an effluent treatment system).
“What level of water quality must be achieved?” or “How to close the gap?”
Finally, determine the treatment levels required for the selected applications by measuring current wastewater quality to establish a baseline and then compare that to the quality level required for the selected applications. This gap in water quality will determine the treatment intensity.
In theory, it’s possible to recover most wastewater. However, some will require more complex process equipment than others, and in a lot of circumstances, a pilot project and trial will determine the best solution.
Conclusions to help industry meet its water usage goals
The most challenging water treatment problems can be addressed and solved by skilled, experienced engineers with access to the innovative processes and technologies needed to build water reuse systems tailored to meet specific objectives, complying with each application’s required specifications. Partnering with an experienced provider like Envirogen to consult on the process can help manufacturers position themselves as leaders in the industry, bringing a positive brand image and growth to those companies that embrace the challenges ahead. Being an environmentally conscious company goes hand-in-hand with profitability.
With corporate and social responsibility, good governance, consumer pressure and related financial performance in mind, I suggest manufacturers lagging in these areas might want to turn their attention, or more of their attention, to these opportunities. Industry has a key role to play in reducing problems associated with chronic water shortages; some caused at least in part by players in the sector.
To reflect the headline of this article – water recycling and reuse can help industry meet water usage goals and much more, all through building a water-resilient business model appropriate to each sector.
Sources/References:
* OECD Environmental Outlook to 2050: “The Consequences of Inaction – Key Facts and Figures”
Could the implementation of industrial water recycling systems and process filtration solutions assist you in achieving your water usage goals?