During 2014 Princes heavily invested in new ingredients processing, warehousing and processing centre. To keep pace with this level of investment and growth, a new water treatment system was required. A scope of works was developed for the soft drink production project during 2017. The proposed system at Princes Soft Drinks, Bradford, needed to conform to hygienic design with the use of EHEDG required throughout. As the system would be used to produce soft drinks for some of the biggest retailers in the UK, the quality of the finish needed to be of the highest standards. A bespoke design was required as an existing patch of land was due to house the plant in a newly constructed building.
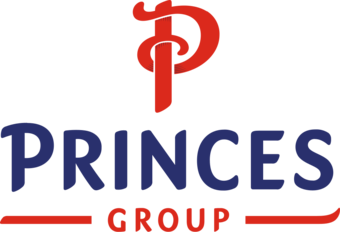
Envirogen Group’s use of 3D model and market leading expertise withing the food and beverage industry meant we were selected to work with this soft drink production customer in delivering a system that would meet all their objectives.
Working together and improving systems
The Challenge
Envirogen’s scope of supply included triplex carbon filters, feed pump system and UV treatment. A production capacity of 300m3/hr was to be delivered through steam sterilising media beds.
The installed system is fully automated inclusive of sterilisation sequences. UV treatment is continuous and monitored in real-time throughout production cycles. A Siemens PLC system and an associated SCADA package were utilised to match the end users’ standards.
Envirogen utilised 3D modelling through the design phase due to the limitation on space to house the system once complete. This approach allowed for input from all stakeholders during the construction of the building.
Once Envirogen were given access for construction the design was finalised and ready to go. This approach facilitated an effective construction and commissioning program.
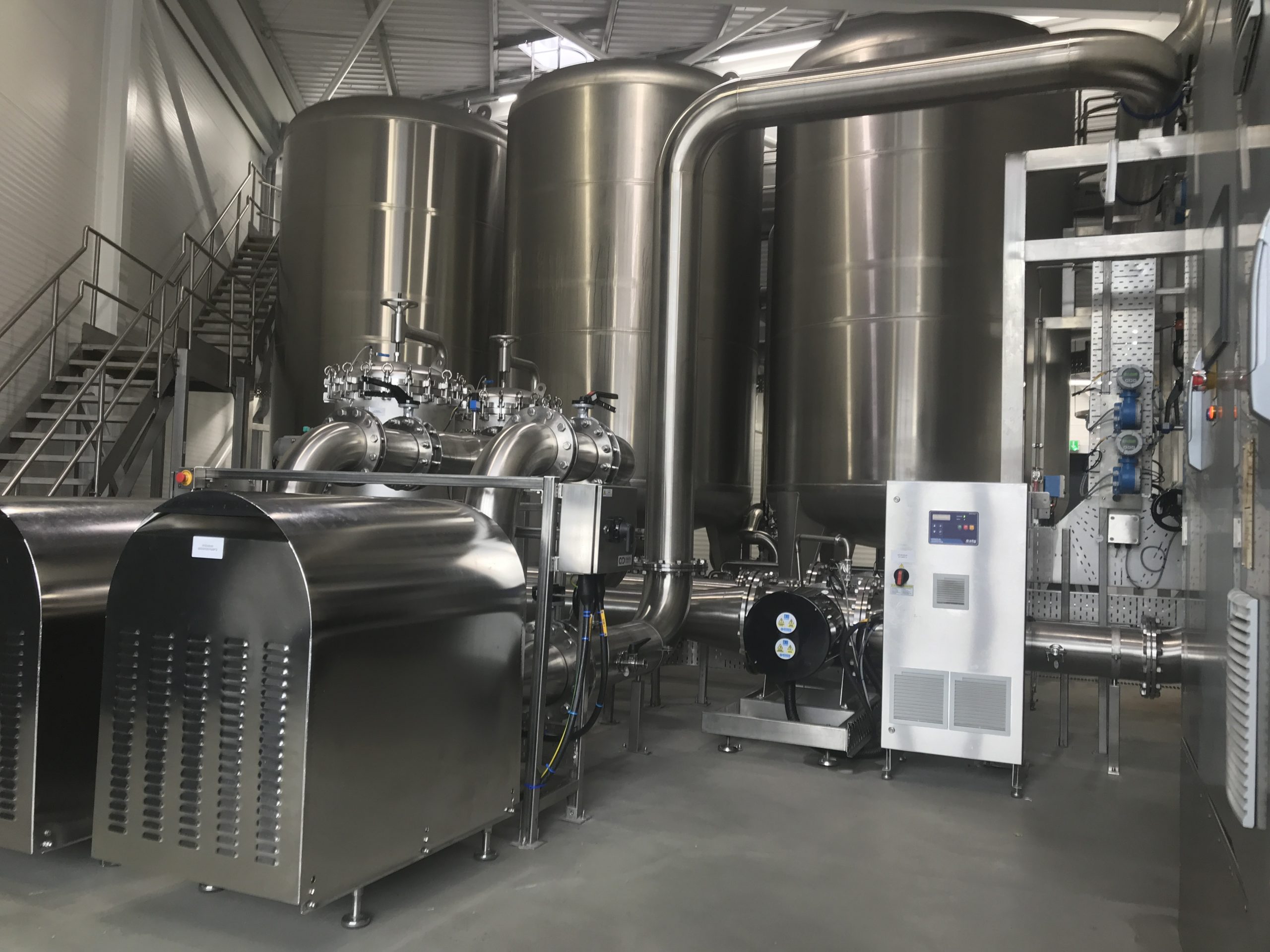
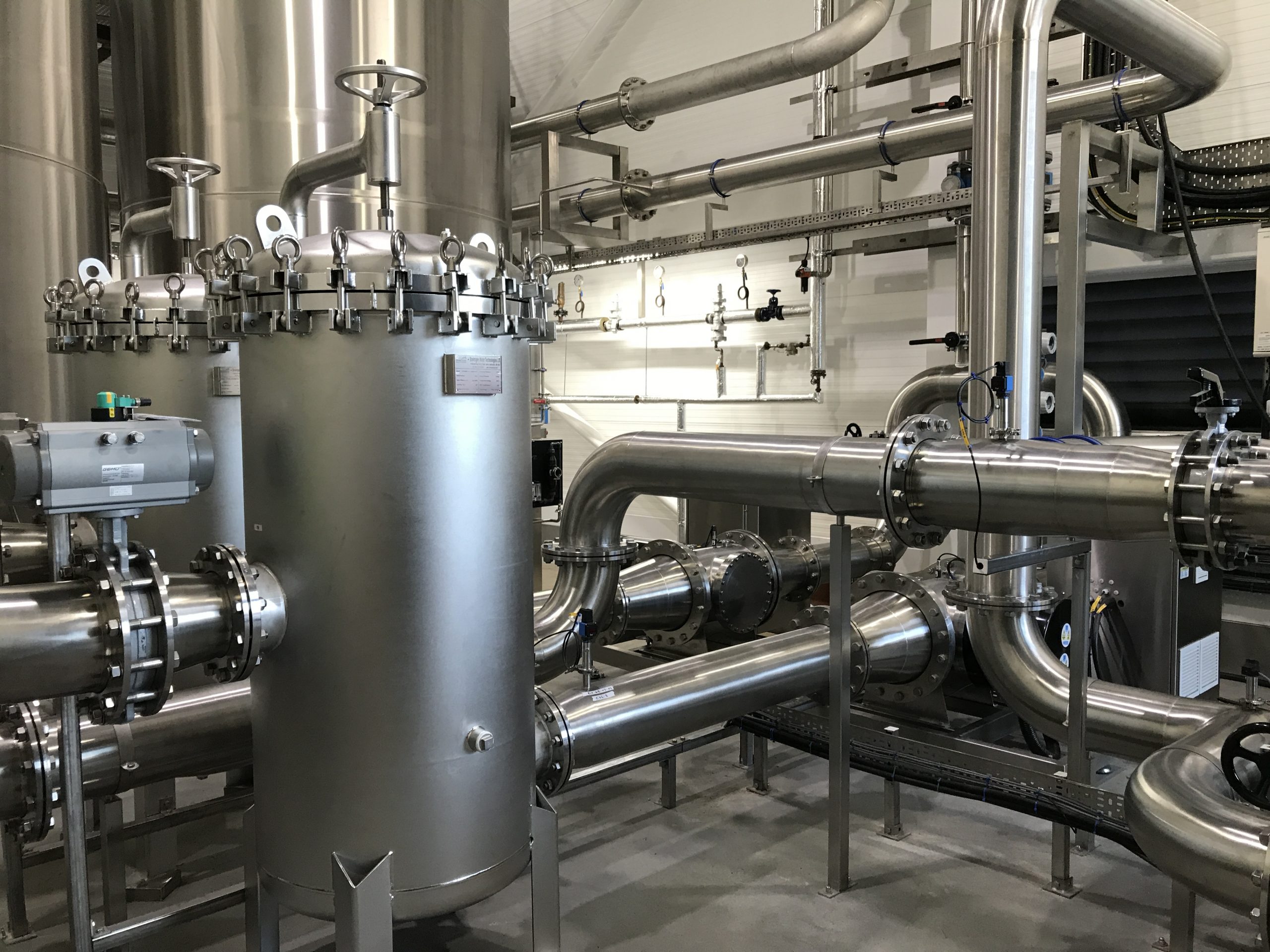
The solution
A triplex activated carbon system was installed on-site
• The system is constructed completely from 316l stainless steel, with all components and vessel coming complete with a polished finished that ensures the system deliveries a high specification finish throughout.
• The plant is fully automated with process monitoring ensuring the correct contact times, UV dose rates, and temperatures during sterilisation.
• During the commissioning phase the product water was tested to ensure the quality matched the stringent specifications assigned to the plant performance criteria.
• Installed system is fully automated inclusive of sterilisation sequences.
Dedicated UK based project management offered a single point of contact to the client throughout the execution phase. The assigned project manager was supported by the wider Envirogen team that consisted of controls engineers, process engineers, and the commissioning team.
For a free assessment to evaluate water treatment and process filtration solutions for your site, contact our team of expert engineers
About the client
With a global supply network and a portfolio of branded and customer own brand products, Princes Group is one of Europe’s largest food and drink groups. Bradford is home to their largest UK soft drinks production site and is a centre of excellence for fruit squash, manufacturing products for Jucee, Geebee and Wells brands. Princes also produce a wide range of customer own brand squash products including cordials, premium high juice and standard squash.
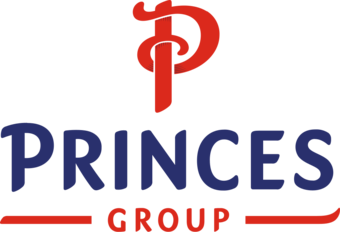