J. Wray & Nephew Limited (a subsidiary of the Campari Group), knew the Jamaican based winery needed to improve the efficiency and productivity of its filtration process and reduce its waste disposal costs. They chose Envirogen Group due to our expertise in crossflow microfiltration technology which reduced production times by nine days. Additionally, through diafiltration, they reduced effluent waste volume, along with recovering a significant amount of the alcohol and chemicals in the waste stream. This meant waste disposal costs were reduced and environmental issues successfully addressed.

Previous process
The previous process involved 90,000 litres of wine being fermented into 100,000 litre holding vessels. The fermentation process took nine days, once fermented, the wine was fed to a fining vessel where finings were added to force the yeast to settle at the bottom of the vessel. The fining process took a further nine days. The produce then continued through coarse filtration using a horizontal leaf filter and then fortification and sheet filtration prior to bottling. The waste amounted to approximately 10,000 litres per day, containing high levels of wasted alcohol but also chemicals causing potential environmental issues.
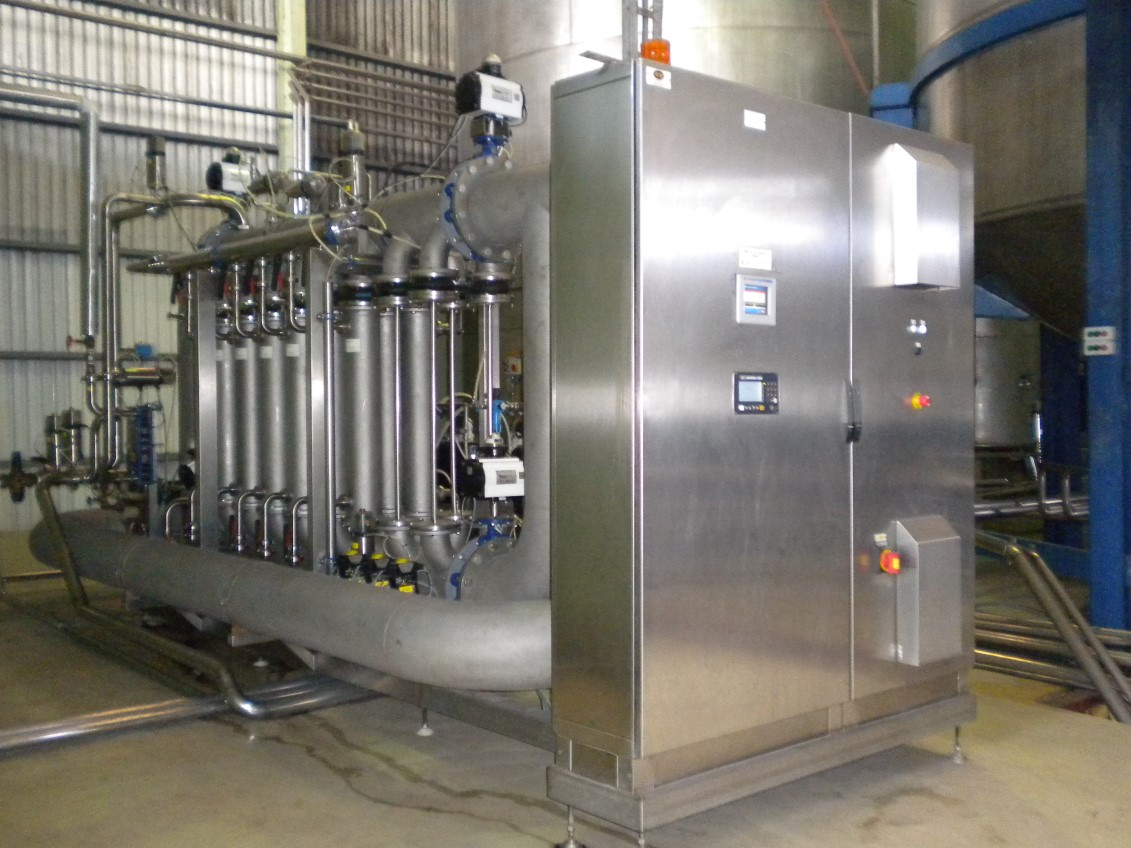
Process improvements cut production time by nine days whilst also reducing costs and addressing environmental impact
We recommended using PureFlow CrossFlow microfiltration and diafiltration technology. Using this in place of the fining stage removed a full nine days from the production process as well as solid removal phase and the horizontal leaf filtration stages. Sheet filtration was then only necessary depending on the requirements of each product.
Not only did our PureFlow CrossFlow significantly reduce production time, but through diafiltration, it also reduced the quantity of the waste, along with recovering a significant amount of the alcohol and chemicals in the waste stream. This meant the cost of waste disposal was reduced and the environmental impact lessened.
Process automation
A fully automated clean in place (CIP) function was also installed on the vessels, enabling, the cleaning of the microfilter as well as the feed vessels. The microfilter feeds into two bright vessels. An automated gas chase was installed to clear the pipes of any remaining residual.
Previously, connections and valves were set manually with personnel physically setting the filtration routes. The new solution meant that the pipework was fabricated stainless steel, with double seat mixed proof valves and is fully automated.
We installed a fully flexible HMI system that allows minimal manual input and from the touch of a button. It means that product runs, ingredients, batch settings, fermentation etc. can be pre-programmed or altered where necessary. The HMI System also offers data from the last ten production runs including: the operator, time, date, fermenter used, bright tank vessel used and so on.
A central supervisory control and data acquisition (SCADA) system was installed so that the site can monitor the entire process filtration operation. It gives a real time graphical representation of what is happening on the floor. It also has the functionality to run reports on the last 10 filter runs and download into Excel. This is constantly logging up to a couple of hundred runs, giving tighter management control. The automated HMI and SCADA system can be accessed remotely by the Envirogen’s own engineers, using an IP address into the PLC which offered enhanced post commissioning optimisation and after sales service support functionality.
Key outcomes
- PureFlow CrossFlow microfiltration technology significantly reduced number of production days needed to complete process (nine days).
- Additional productivity efficiencies gained from the solid removal phase and horizontal leaf filtration stages.
- Diafiltration to reduce quantity of waste, along with recovering a significant amount of the alcohol and chemicals in the waste stream to reduce environmental impact.
- No operation downtime, with filtration process integrated seamlessly to production operations.
- Control panels ensure full visibility and management for all systems.
For a free assessment to evaluate water treatment and process filtration solutions for your site, contact our team of expert engineers
About the client
J. Wray & Nephew Limited is a subsidiary of the Campari Group, a major player in the global branded beverage industry, with a portfolio of over 50 premium and super premium brands marketed and distributed in over 190 countries worldwide. The Company has Jamaica’s largest wine and spirits portfolio, comprising a number of owned and represented brands including the iconic Wray and Nephew White Overproof Rum and Appleton Estate Jamaica Rum.
